F1 News: Aston Martin team already shipping equipment to tracks
Head of Aston Martin F1 Race and Trackside Logistics Franco Massaro lifts the lid on their sea freight operation and why 2025 started for him and the team months ago.
The 2025 Formula One season doesn’t start until March but, for Franco Massaro and his colleagues in the Race and Trackside Logistics team, the new campaign has been in full swing for months already.
Another 24-race marathon awaits this year, and while personnel and cars will travel to most race locations just a handful of days before each event, much of the equipment the team needs for the early-season races is already in transit at sea.
As they gear up for the 2025 season, Franco sheds light on what’s going where and how it gets there.
THE NUMBERS GAME
“We have six identical sets of equipment, worth circa £2 million each, and most of that comprises garage infrastructure rather than car parts, such as paneling, timing stands, the center island, and air conditioning.
“Each set consists of five 40ft containers of garage equipment and two 40ft containers of hospitality equipment, with each set consisting of around 100 cases and steel stillages of various sizes. The weight of the five garage containers is about 40 tonnes, and the two hospitality containers are a little bit lighter: around 10-12 tonnes between them.
“The amount we carry has also grown because air freight costs have risen, so we’ve looked at what we can take out of our air freight that goes from race to race and put that into sea freight, and then we’ve manufactured a few extra bits of equipment. Essentially, we have more sets of equipment doing around four races a year, rather than one set getting flown to every race.
“It’s cost-effective. Say a timing stand weighs 1,000kg, it saves us nearly £250,000 over a season by putting it into sea freight. Obviously, you’ve then got to produce more of them to cover the season, but you’re looking at payback within one to two years because most equipment has a life of around 5-10 years.
“We navigate all the overseas events of the year with these sets and two of them will support the garage requirements for European events.”
FROM PORT TO TRACK
“To move everything door-to-door, there are two logistics companies that help F1 teams move their freight: DHL and RPM. We contract one of them, currently RPM, to collect our items from our sea freight facility, load and take them to port, and when it arrives the other side it’s trucked to the circuit.
“The aim is for it to arrive at track approximately 10 days before the race itself, so usually a Thursday or Friday, and it’s then positioned for each team around the garages. The sensitive and non-waterproof equipment is put inside the garage and the rest is left outside. Then an early build crew arrives on Saturday to begin assembly.”
LOGISTICAL CHALLENGES
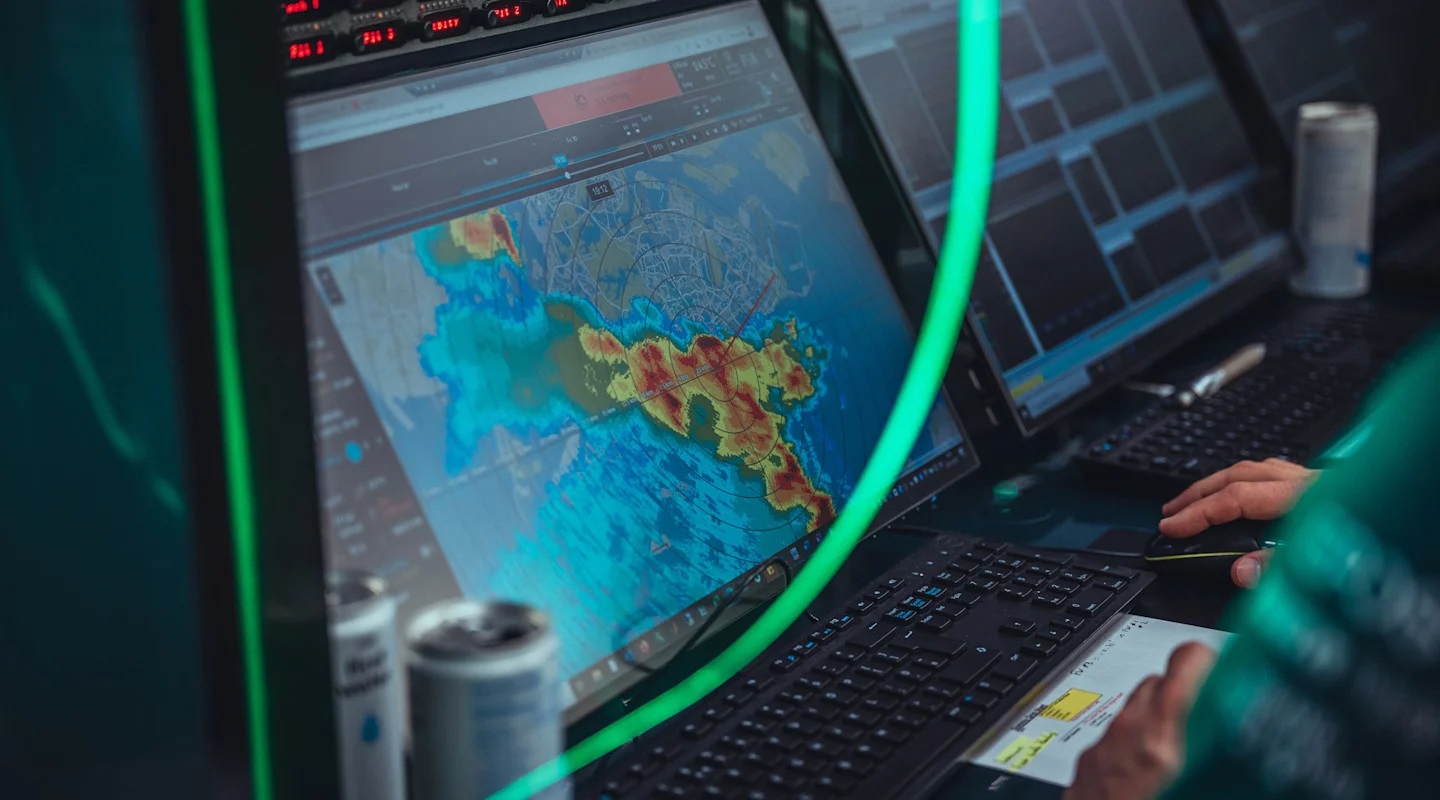
“When you’re moving freight around the world, you’re always going to face a variety of challenges.
“For example, there have been issues with cargo vessels being targeted in the Red Sea and Suez Canal by groups simply wanting to disrupt service. A lot of shipping lines have taken action to avoid the area altogether. Instead, they’ve been going around the Cape of Good Hope, at the bottom of South Africa, which is a lot of miles and time added on to transit – and is something we need to factor into our plans. Case in point, at the beginning of 2024, we sent our freight to Japan via the US. You wouldn’t normally go that way because that adds considerable journey time.
“Additionally, shipping lines aren’t like airlines: you have to build in a lot of extra time to make sure your sea freight arrives on schedule because they can suddenly change plans. It gets quite difficult if the line decides the vessel isn’t going to stop at a particular port, or they’re going to change route, because the Aston Martin team doesn’t have a lot of control over that. Fortunately, we can request for our containers to be removed so we can change our plans and our logistics partner helps with that too, but we’re always trying to allow for that eventuality by building in extra time.
“We’re always monitoring where our freight is. When we get the vessel number for the ship carrying our freight, we can see where it is in the world. Sometimes you see it going from port to port, collecting cargo, and you’re thinking is it ever going to come out of a certain area. I’ve got a bit obsessed with online shipping trackers. It gets quite addictive after a while!
“Weather can also create problems. Luckily, we were not affected by the weather in 2024, but some of the storms around the United States Grand Prix last year did impact some of the freight going there. Some vessels changed routes and the cargo had to be offloaded and trucked in.
“The length of the calendar also provides its own challenges. When I started – I’ve been here nearly 22 years – we had October through to December to service everything for the next year, but now there’s next to no time to do that.
“Our sets are very rarely in the UK and there are lots of items that need servicing so we’ve been reviewing our service plans. Where we’d service things just at the end of the season, we’re now servicing whenever we get an opportunity during the year.
“Obviously, the worst-case scenario is something happens at sea and the vessel’s delayed to the point where it’s not going to make the event. Fortunately, we haven’t had that happen.”
CHARTING A COURSE
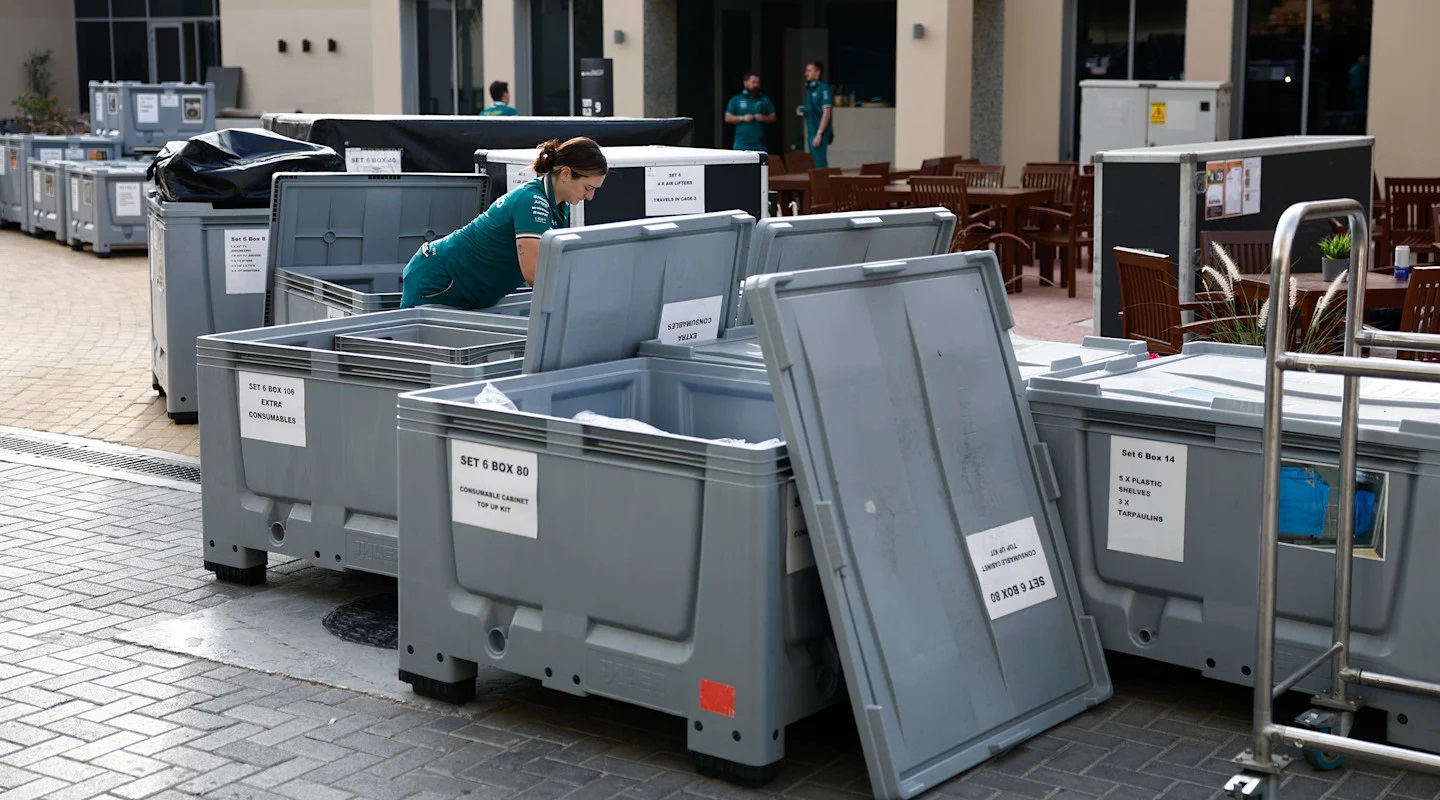
“As soon as the calendar comes out for the following season, myself, Chris Dodd, Aston Martin Race Team Operations Coordinator, and Dale Magorrian, Aston Martin Race Team Support, look at how we’ll manage it with the sets we’ve got and where issues may arise and then we liaise with our logistics partner RPM.
“We began working on our 2025 plans back in July 2024 alongside RPM. As soon the 2025 calendar came out, we started piecing it together and picking out where some of the difficulties might be. We gave RPM a few weeks to mull it over and then we met before the summer shutdown. This is what we devised:
Set 1
“The containers that were in Mexico for 2024 are en route to China. Our preference would have been to bring it all back to the UK for a service, but by the time it would have reached the UK, we wouldn’t have had the time before it needed to depart again.
“At some point in the next few weeks, it will end up in a storage facility for a little while. In this case, it is on a very slow boat to China, but it will still arrive early enough to need storing.
“Once the Chinese Grand Prix is finished, it will head to North America for the races in Miami and Montréal, and then we’ll bring it home for a service before the latter part of the year.”
Set 2
“The equipment from Qatar 2024 is on its way to Australia. It will be at sea for a reasonable length of time and won’t be in storage for too long. Once the Australian Grand Prix is complete, it will make its way home to the UK where we’ll service it and then send it back out.”
Set 3
“The Abu Dhabi 2024 set will sit in storage for a period in Bahrain, because it’s not had to travel far. We’ll use it both for the pre-season test and the race in Bahrain before it comes back to the UK for service. It will then support the fly-aways in the final part of the season.”
Set 4
“The Japan-bound set came back from the 2024 Azerbaijan Grand Prix fairly quickly and was serviced and loaded ahead of the winter shutdown before departing once more. Following the Japanese Grand Prix, it will make its way back to the UK before we prepare it for the remainder of the year.”
Set 5
“This set is on its way home from Brazil and we expect it back imminently. As soon as it arrives, we’ll prepare it for Saudi Arabia and then it will come back to the UK before it supports some of the European events – namely the Monaco, Austrian, Hungarian, and Italian Grands Prix.”
Set 6
“This set is also on its way home, this time from Las Vegas, and we expect it back a little later in January. We’ll prepare it for the first European race of the season in Imola and it will also support the races in Spain, Britain, Belgium, and the Netherlands.”
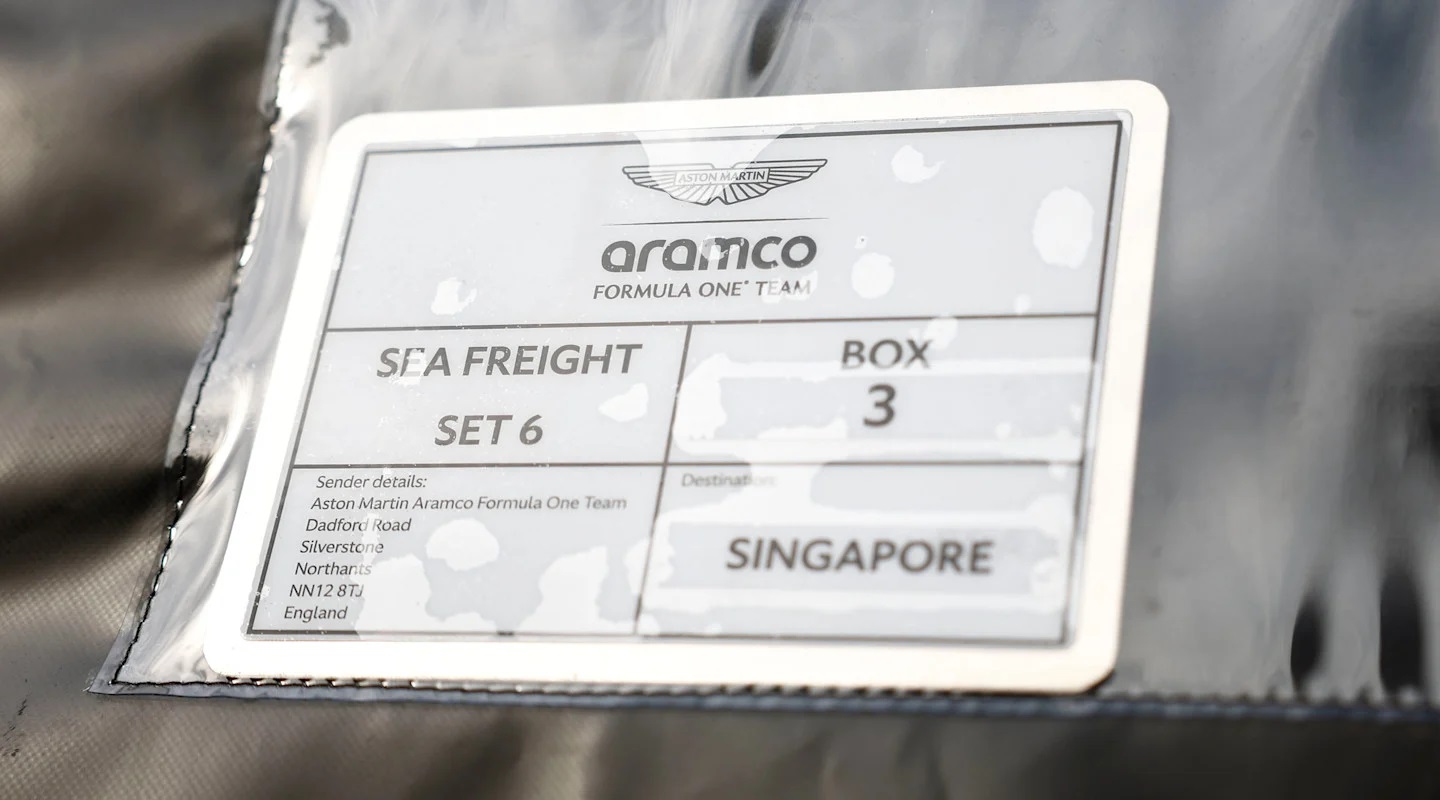
LOOKING FURTHER FORWARD
“We’ve got up to the 2025 Italian Grand Prix finalized and very soon we’ll confirm our plans for the rest of the season because, as soon as the ’26 calendar comes out, we’ll be working on that. In fact, we’ve already identified one potential challenge then.
“The news of the Canadian Grand Prix moving to May from 2026 may cause us a headache, as there’s a chance it could end up forming a double-header after the race in Miami. In this case, we wouldn’t have time to truck the freight up from Miami to Montréal and we also don’t want to have two separate freight sets in North America at the same time.
“But for now, that’s not certain. Whatever happens, when the 2026 calendar is official, our process will start and we’ll piece together the puzzle once more.”