F1: The FIA explains their crackdown on bodywork flexing
The FIA is introducing a number of clarifications around F1 bodywork flexibility to provide a clearer framework for teams to work within.
At this weekend’s FIA Formula 1 Singapore Grand Prix, the FIA is introducing a new Technical Directive regarding the aerodynamic influence offered by particular components, and while directives are advisory and do not constitute Technical Regulations, they form a key element of the Federation’s application of the rules – providing clarity, ensuring compliance and promoting fairness.
In the case of TD018, the clarity is provided around bodywork design details and in particular, front and rear wings that, according to FIA Single Seater Technical Director Tim Goss “try to get the most out of the boundaries that exist within the regulations”.
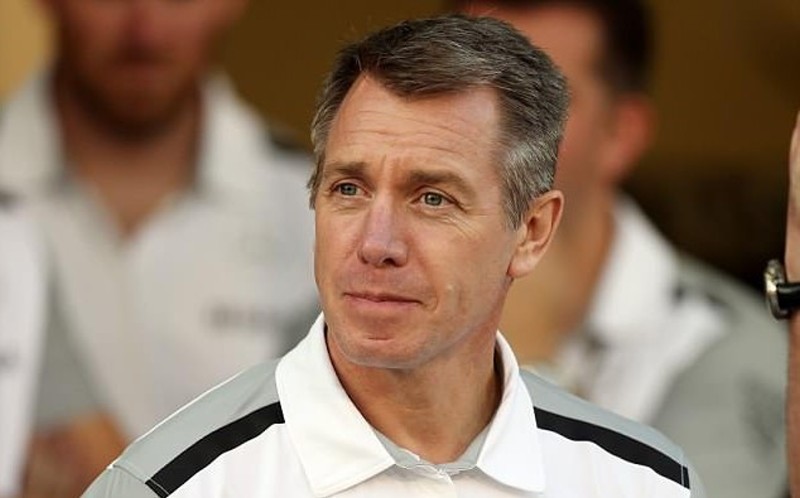
“There are a lot of clever engineers out there looking to get the most out of the regulations, and we have to make sure that everyone has a common understanding of where the boundaries are, and we have to be fair and balanced across the whole group in how we apply them,” he says. “And in recent times we have seen a little bit too much freedom being applied to the design details of aerodynamic components.”
In the new directive, Goss says that the FIA became aware of a number of cases where bodywork designs (in particular, front and rear wing designs), comply with the requirements of Article 3.15 of the Technical Regulations, governing Aerodynamic Component Flexibility, but which could be deemed to contravene the provisions of Article 3.2.2, because they “exploit regions of purposely designed localized compliance and/or relative motion between adjacent components”.
In layman’s terms, as Goss explains, it means that clearer guidance around how components are joined together needed to be given.
“For us, the important bit of Article 3.2.2 is that ‘all aerodynamic components or bodywork, influencing the car’s aerodynamic performance must be rigidly secured and immobile with respect to their frame of reference and that they must make use a uniform, solid, hard, continuous surface under all circumstances’,” he explains. “Now, quite clearly things cannot be totally rigid.
“So, we have a range of load deflection tests that define how much elements can bend and we’ve evolved those tests to represent what the teams are trying to achieve on track and to put a sensible limit on them.
“We play by those rules, while teams look to exploit the allowance in terms of deflection. That’s normal. So the TD is just about making sure that we, the FIA, and the teams, all have a common understanding of where we will draw the line in terms of these design details.”
And according to TD018 that line now exists at point where “regardless of conformity with the load tests defined in Article 3.15 [the FIA] would consider any design which uses the relative motion between adjacent components of mechanisms in order to maximize aerodynamic deformation to be in breach of Article 3.2.2.
“What we don’t want to see,” says Goss, “as an example, is that the joint of a rear beam wing and an end plate is decoupled in any way such that it rotates about a pivot there, or that it can move laterally or up and down.”
Advisories such as the one being made this weekend often stem from questions being asked about the legality of one team’s car by a rival, but in the case of TD018, Goss explains that guidance is being issued in response to a broader recognition that more clarity was needed.
“It’s not that we’ve seen any one particular car or feature that we’ve targeted, or an element that’s been common across the whole grid,” he says.
“This is about where front and rear wing elements join the nose, join the rear impact structure, join the rear wing endplates.
“And there have been several instances where teams have tried to make the most of the deflection allowance by permitting some bits and pieces to start moving relative to each other. And if you’ve allowed one piece to be decoupled relative to another, the bodywork might have to have some degree of local flexibility at that location.
“And if there is local flexibility, we’re saying, clearly, that’s not compliant with being uniform, solid, hard and continuous. Under the TD, we have included various examples, designs which we consider are not permitted and exceptions which we consider are permitted.”
To illustrate the grid-wide need for clarity, the FIA technical department issued a draft version of the directive to teams, asking for further feedback before finalizing the advisory.
“With matters such as this, we issue the TD in draft form,” explains Goss.
“We’ve been speaking to some teams for several weeks where we believed there was a need for clarity, and then issued our proposal to all teams asking for feedback by the 29th of August.
“We then spoke again in Monza, about design details, where teams were asking us about examples. It’s just a matter of fairness to everyone, making sure we all have that common understanding, and that everyone knows how we are going to operate from a given date.”
To ensure further transparency going forward the FIA is to also begin requesting additional drawings of the structural designs of areas of concern.
“Teams have to submit designs at the moment, they upload lots of information, but now they will have to upload structural connections and that in itself helps to self-police it.”
And ultimately, the FIA Single-Seater Technical Director says that advisories such as Technical Directive 018 are a hugely important mechanism through which the F1’s rule maker can effectively and progressively guarantee fairness.
“This Technical Directive is an example of where ourselves and the teams work together to try and make sure that we have a common understanding, and it is a huge positive,” he says. “It’s not simple, but if we can evolve that understanding in a sensible, considered way then I think we’re going in the right direction.”
Latest Technical Regulations of Aerodynamic Components
Revised 31 August 2023.
ARTICLE 3: AERODYNAMIC COMPONENTS
3.1 Definitions
3.1.1 Aerodynamic Components or Bodywork
All parts of the car in contact with the external air stream.
- The following components are considered to be bodywork:
- all components described in Article 3;
- inlet or outlet ducts for the purpose of cooling, up to the component they are intended to provide cooling for;
- inlet ducts for the power unit (air boxes) up to the air filter;
- primary heat exchangers, as defined in Article 7.4.1 (b).
- The following components are not considered to be bodywork:
- cameras and camera housings, as defined in Article 17;
- rear view mirrors as defined in Article 2;
- the ERS status light;
- parts definitely associated with the mechanical functioning of the power train, transmission of power to the wheels, and the steering system providing, in any case, none are of a design contrived to achieve an aerodynamic effect;
- the wheel rims and tires;
- the brake disc assemblies, calipers and
3.1.2 Frame of Reference
The geometry, component or group of components with respect to which certain bodywork must remain immobile.
3.1.3 External air stream
The flow of air around the car which has a primary impact on its aerodynamic performance.
3.1.4 Concave and convex curvature
References made in this Article on curvature of aerodynamic surfaces refer to the part of the aerodynamic surface which is in contact with the external air stream.
When references are made to the curvature of a surface, without specifying an intersection with a particular plane, the local curvature at any point will be defined as the curvature of the intersection of the surface in question with a plane passing through a line normal to the surface at that point. The concave radius of curvature of the surface at that point will be defined as the minimum concave radius of curvature obtained when the intersecting plane is swept through 180 degrees around the normal line. The convex radius of curvature of that surface at that point will be defined as the minimum convex radius of curvature obtained when the intersecting plane is swept through 180 degrees around the normal line.
As an example, and for the sake of clarity, the aerodynamic surface of a solid sphere would be the surface where this sphere makes contact with the external airstream, and would be considered to be a convex surface.
3.1.5 Normal to an aerodynamic surface or curve
The normal applied to an aerodynamic surface at a given point is a vector which is perpendicular to the surface at that point and points towards the local external air stream.
The normal to a curve at a given point will be considered to be the normal to the surface containing the curve at the same point.
3.1.6 Tangency Continuity
Tangency Continuity at a given point of a curve or at a given point of a surface, is satisfied if the value of the tangent is continuous.
Tangency Continuity at intersections between two curves or two surfaces, is satisfied if the two curves or two surfaces at the intersection are tangent to one another and also have their normal coincident with each other.
Where two adjacent surfaces are not tangent continuous but could be made so by applying an edge radius of no more than 1mm along their boundary, these surfaces will be considered tangent continuous at this boundary whether or not the edge radius is applied, as long as such an edge radius is permitted according to the relevant article.
3.1.7 Curvature Continuity
Curvature Continuity between two curves, at a given point of a curve, between two surfaces or within a surface is satisfied if the value of the curvature is continuous and in the same direction.
3.1.8 Open and closed sections
Within the prescribed limitations of the relevant regulation, a section through the bodywork when intersected with a defined plane will be considered closed if it forms a complete boundary by itself otherwise it will be considered open.
3.1.9 Fillet and Edge Radius
A fillet radius is formed by rounding an internal corner (included angle less than 180 degrees) with a concave surface by only adding material, whilst an edge radius is created by smoothing an external corner (included angle greater than 180 degrees) with a convex surface by only removing material.
In both cases the resultant surface must be formed by arcs with radius of curvature respecting the limit(s) specified, connecting two fully defined surfaces tangentially with no inflection and perpendicular to the intersection between them. Unless otherwise specified, both fillet and edge radii may change in magnitude around the periphery of the boundary around which they are defined, but such changes must be continuous.
If there exists a discontinuity in tangency at the trailing edge of the intersection between the parts to be joined by a fillet radius, then a closed aerodynamic fairing may be added immediately behind the trailing edge. This fairing must be no larger in cross section than the preceding fillet radius and any trailing edge immediately adjacent to the fillet and no longer than three times the maximum fillet arc radius at this point.
3.1.10 Aerodynamic seal
The function by which the flow between two regions of different pressure is kept to the minimum feasible magnitude.
3.1.11 Gurney
A component fitted to the trailing edge of a profile in order to adjust its aerodynamic performance. In any plane normal to the trailing edge of the profile, the Gurney must contain a flat section no more than 1mm thick, and of a given height (defined as the size of the Gurney), and a bonding flange onto the surface of the wing which may be no more than 20mm long and 1mm thick. No part of the Gurney may protrude behind a line that is normal to the surface on which the Gurney is applied at the point of the trailing edge of the profile.
3.2 General Principles and Legality Checking
3.2.1 Objective of Article 3
An important objective of the Regulations in Article 3 is to enable cars to race closely, by ensuring that the aerodynamic performance loss of a car following another car is kept to a minimum. In order to verify whether this objective has been achieved, Competitors may be required on request to supply the FIA with any relevant information.
In any case the Intellectual Property of this information, will remain the property of the Competitor, will be protected and not divulged to any third party.
3.2.2 Aerodynamic Influence
With the exception of the driver adjustable bodywork described in Article 3.10.10 (in addition to minimal parts solely associated with its actuation) and the flexible seals specifically permitted by Articles 3.13 and 3.14.4, all aerodynamic components or bodywork influencing the car’s aerodynamic performance must be rigidly secured and immobile with respect to their frame of reference defined in Article 3.3. Furthermore, these components must produce a uniform, solid, hard, continuous, impervious surface under all circumstances.
Any device or construction that is designed to bridge the gap between the sprung part of the car and the ground is prohibited under all circumstances.
With the exception of the parts necessary for the adjustment described in Article 3.10.10, or any incidental movement due to the steering system, any car system, device or procedure which uses driver movement as a means of altering the aerodynamic characteristics of the car is prohibited.
The Aerodynamic influence of any component of the car not considered to be bodywork must be incidental to its main function. Any design which aims to maximize such an aerodynamic influence is prohibited.
3.2.3 Symmetry
All bodywork must be nominally symmetrical with respect to Y=0. Consequently, and unless otherwise specified, any regulation in Article 3 concerning one side of the car will be assumed to be valid for the other side of the car and references to maximum permissible numbers of components in Article 3 will also refer to the one side of the car.
Minimal exceptions to the requirement of symmetry of this Article will be accepted for the installation of non-symmetrical mechanical components of the car, for asymmetrical cooling requirements or for asymmetrical angle adjustment of the front flap defined in Article 3.9.7.
Bodywork on the unsprung mass must respect this Article when the suspension position of each wheel is virtually re-orientated so that its wheel coordinate system axes (described in Article 2.11.3) are parallel to their respective axis of the car coordinate system (described in Article 2.11.1).
3.2.4 Digital legality checking
The assessment of the car’s compliance with the Aerodynamic Regulations will be carried out digitally using CAD models provided by the teams. In these models:
- Components may only be designed to the edge of a Reference Volume or with a precise geometrical feature, or to the limit of a geometrical criterion (save for the normal round-off discrepancies of the CAD system), when the regulations specifically require an aspect of the bodywork to be designed to this limit, or it can be demonstrated that the design does not rely on lying exactly on this limit to conform to the regulations, such that it is possible for the physical bodywork to
- Components which must follow a precise shape, surface or plane must be designed without any tolerance, save for the normal round-off discrepancies of the CAD
3.2.5 Physical legality checking
The cars may be measured during a Competition in order to check their conformance to the CAD models discussed in Article 3.2.4 and to ensure they remain inside the Reference Volumes.
- Unless otherwise specified, a tolerance of ±3mm will be accepted for manufacturing purposes only with respect to the CAD surfaces. Where measured surfaces lie outside of this tolerance but remain within the Reference Volumes, a Competitor may be required to provide additional information (e.g. revised CAD geometry) to demonstrate compliance with the regulations. Any discrepancies contrived to create a special aerodynamic effect or surface finish will not be
- Irrespective of a), geometrical discrepancies at the limits of the Reference Volumes must be such that the measured component remains inside the Reference
- A positional tolerance of +/- 2mm will be accepted for the Front Wing Bodywork, Rear Wing Bodywork, Exhaust Tailpipe, Floor Bodywork behind XR=0, and Tail. This will be assessed by realigning each of the groups of Reference Volumes and Reference Surfaces that define the assemblies, by up to 2mm from their original position, to best fit the measured
- Irrespective of b), a tolerance of Z=+/-2mm will be accepted for parts of the car lying on the Z=0 plane, with -375 ≤ Y ≤ 375 and ahead of XR=0.
- Minimal discrepancies from the CAD surfaces will also be accepted in the following cases:
- Minimal repairs carried out on aerodynamic components and approved by the FIA
- Tape, provided it does not achieve an aerodynamic effect otherwise not permitted by Article 3
- Junctions between bodywork panels
- Local bodywork fixing details
3.2.6 Datum Points
All cars must be equipped with mountings for optical targets that enable the car’s datum to be determined for scrutineering in the following locations:
- One on the forward part of the top of the survival
- Two positioned symmetrically about Y=0 on the top of the survival cell close to XB=0.
- Two positioned symmetrically about Y=0 on the side of the survival cell close to XB=0.
- Two positioned symmetrically about Y=0 on the side of the survival cell close to the rear mounts of the secondary roll
- Two positioned symmetrically about Y=0 within an axis-aligned cuboid with an interior diagonal defined by points [XC=0, 175, 970] and [XC=150, -175, 870].
- One probed point on the RIS or gearbox
In all cases, a file with required datum points must be supplied for each survival cell.
For deflection testing, all cars must be provided with a means of mounting a reference artefact to the RIS. This mounting may be temporary, but must be rigid with respect to the underlying car structure.
Full details of the requirements are given in the Appendix the Technical and Sporting Regulations.
- Section titles and Article titles within this article have no regulatory
- Static pressure tappings are permitted in surfaces, provided that they;
- Have an internal diameter of no more than
- They are flush with the underlying
- Are only connected to pressure sensors, or are blanked, without
3.3 Component Definition
The permitted bodywork and the relevant frame of reference (as defined in Article 3.1.2, and used to establish compliance with Article 3.2.2) for each group is defined in the following Articles 3.3.1, 3.3.2 and 3.3.3.
3.3.1 Bodywork which is part of the sprung mass of the car
The only sprung mass bodywork permitted is that defined under Articles 3.5 to 3.12 and under Articles 3.1.1.a.ii to iv. The frame of reference for every part of the car classified as Sprung Mass Bodywork is the coordinate system defined in Article 2.11.1.
Any bodywork that is trimmed or filleted in Article 3.11 must first be declared as belonging to one of the groups defined in Articles 3.5 to 3.10.
Unless otherwise stated, the compliance of an individual bodywork group to Article 3 will be assessed independently and prior to any trimming, filleting and assembly operation referred to in Article 3.11, and the FIA may request to see any discarded geometry after final assembly. Once the final assembly is completed, any bodywork surfaces no longer exposed to an external airstream or internal duct may be modified, providing they remain unexposed.
3.3.2 Wheel Bodywork
The only wheel bodywork permitted is that defined under Article 3.13. With the exception of wheel covers, as defined in Article 3.13.7, the frame of reference for every part of the car classified as Wheel Bodywork is the corresponding upright structure and the corresponding coordinate system defined in Article 2.11.3.
The frame of reference for any wheel cover, as defined in Article 3.13.7 is the corresponding wheel rim.
3.3.3 Suspension Fairings
The only suspension fairings permitted are those defined under Article 3.14. In order to assess compliance with Article 3.2.2, the frame of reference of any suspension fairing is the structural suspension member that it is attached to.
3.4 Overall Dimensions
3.4.1 Width
With the exception of the tires, the wheel rims defined in Article 10.7.2, and the wheel covers defined in Article 3.13.7, no part of the car may lie outboard of Y=1000.
3.4.2 Wheelbase
The distance between the planes XF=0 and XR=0 must not exceed 3600mm.
3.4.3 Front Wheel Position
The plane XF=0 must not be behind XA=100.
3.5 Floor
3.5.1 Floor Body
Bodywork declared as “Floor Body” must:
- Lie within RV-FLOOR-BODY.
- Entirely obscure RS-FLOOR-PLAN, and RS-CASSETTE, when viewed from
- Entirely obscure RS-FLOOR-REAR, when viewed from the
- Lie on the reference plane if both visible from below and within the boundaries of RS-FLOOR-MID when viewed from
Furthermore:
- Its complete surface, when intersected with any X-plane must produce only a single section that is continuous, closed and with all parts of the section visible from either above or
- Its complete surface, when intersected with any Y-plane must produce only a single section that is continuous, closed and with all parts of the section visible from either above or below. Two such sections will be permitted outboard of Y=595, provided:
- these two sections are not closer than 50mm to each other on any Y-plane, except for a transition between one and two sections that is contained within two
Y-planes up to 10mm apart.
- the rearward-most point of the forward-most section is aft of XF=1700.
- Its complete surface must be tangent continuous, and any concave radius of curvature must be greater than 25mm. This is with the exception of regions of its surface that are within 60mm of the point [XR, Y, Z] = [-350, 495, 5] and visible from
- Its complete surface must be tangent continuous, and any convex radius of curvature must be greater than 25mm. This is with the exception of regions of its surface that are:
- Within 60mm of the point [XR, Y, Z] = [-350, 495, 5] and visible from
- In plan view, within 5mm of the boundary of the Floor Body. In the region -345 < XR < 440 this exception only applies below Z=
- Visible from above, and within 10mm of the load application points defined in Article 3.15.7.c. Such features must be the minimal required for applying the loads required by that
- All regions of its surface that are visible from above, outboard of Y=500 and forward of XF=1700, must be visible from the
Once the surfaces defined as Floor Body have been defined in accordance to the provisions of parts (a) to (i), it is permitted to attach additional bodywork to the surface of the Floor Body for the purpose of aiding local flow attachment. These items, which need not comply with parts (a) to (i), will nevertheless be considered part of the Floor Body and must:
- Be entirely within 10mm of the surface of the Floor Body that is visible from
- Be entirely within 100mm of the car centre plane and rearward of XR= -550.
- Collectively lie in a region no greater than 50mm when measured in the X-direction.
The requirements of parts (e), (g) and (h) must be satisfied when considering both sides of the car.
3.5.2 Floor Fences
Bodywork declared as “Floor Fences” must lie within RV-FLOOR-FENCE. Furthermore:
- For each Floor Fence, a virtual surface must first be defined, which must:
- Be a single surface with no apertures. Any straight line aligned with the Y-axis must intersect the virtual surface no more than
- Produce no more than one curve when intersected with any Z-plane. At no point along this curve may the line tangent to it subtend an angle greater than 50° to the X-axis. For the virtual surface whose associated Floor Fence is subsequently used to obscure RS-FLOOR-FENCE, the same angle must be no greater than 40°.
- Produce no more than one curve when intersected with any X-plane. At no point along this curve may the line tangent to it subtend an angle greater than 25° to the Z-axis. This curve must not intersect the surface of the Floor Body that is visible from above. If this curve is rearward of XF=960, it must intersect the Floor Body exactly once and any part of the curve above this intersection must be internal to the Floor
- Not be closer than 10mm at any point to any other Floor Fence virtual
- Once the virtual surface has been defined, the associated Floor Fence must:
- Fully enclose the entire virtual
- Be no more than 4mm distant from the virtual surface at any
- There may be no more than four Floor Fences on each side of the car centre plane, one of which must fully obscure RS-FLOOR-FENCE when viewed from the side. The curve produced by intersection of the virtual surface associated with this fence and the Floor
Body, must be fully within 5mm of the boundary of the Floor Body when viewed from above.
- Once each Floor Fence has been fully defined it is permitted to apply a Fillet at the boundary between it and the Floor Body, having radius of curvature no greater than 50mm. Such a Fillet would then be considered part of the associated Floor
- Once the Floor Body, each Floor Fence and each associated Fillet have been fully defined, the boundary of the assembled bodywork between XF=1290 and XR= -700, when viewed from below, must be below Z=35.
3.5.3 Floor Edge Wing
Bodywork declared as “Floor Edge Wing” must:
- Lie within RV-FLOOR-EDGE.
- Be a single volume with no
- Its complete surface, when intersected with any X-plane must produce only a single section that is continuous and closed, having cross-sectional area no greater than 2000mm2. This section must be between 5mm and 20mm distant from the curve produced by intersection of the Floor Body with the same X-plane, at its closest
- Its complete surface, when intersected with any Z-plane must produce only a single section that is continuous and
- Its complete surface must be tangent continuous and any concave radius of curvature must be greater than
For the sole purpose of providing a structural connection between the Floor Edge Wing and the Floor Body, it is permitted to add up to six support brackets per side of the car. These brackets, which need not comply with parts (a) to (e), will nevertheless be considered part of the Floor Edge Wing and must:
- Be in their entirety within 40mm of the Floor Body and 30mm of the Floor Edge
- Be no more than 5mm thick. A fillet radius no greater than 4mm will be permitted where these brackets join to the components they
- Be no larger than 40mm in the X-direction and have no dimension that exceeds
- Not be closer than 50mm at any point to any other such support
- Not be visible from
3.5.4 Bib
Bodywork declared as “Bib” must:
- Lie within RV-BIB.
- Be a single volume with no
Furthermore, when considering both sides of the car, its complete surface must:
- When intersected with any X plane produce only a single section that is continuous, closed and with all parts of the section visible from either above or
- Be tangent continuous with no concave radius of curvature when viewed from below and any concave radius of curvature when viewed from above must be greater than 15mm.
- Not contain any convex radius of curvature less than 15mm. This is with the exception of regions of its surface below Z=5 that are within 5mm of any point that, when viewed from above, lies on the boundary of the
3.5.5 Bib to Floor Body Assembly
Once the Bib and Floor Body are fully defined, the Bib and the Floor Body must be trimmed to each other, to create one unified volume with no remaining overlapping surfaces. A fillet radius, no greater than 50mm, may be applied along the intersection between these surfaces.
This fillet, which need not comply with Article 3.5.4, will nevertheless be considered part of the Bib.
Furthermore, in the area of the fillet, minimum flexibility is permitted in order to allow compliance of the Front Floor Structure when the front of the car comes into contact with the ground. After the fillet has been applied, the external surfaces at the boundaries between adjacent sections of Bib and Floor Body must maintain both continuity and tangency in any X, Y, or Z plane.
3.5.6 Floor Bodywork Group
Once the components defined in Articles 3.5.1 to 3.5.5 have been constructed in accordance to the provisions of those Articles, and any subsequent operation of sub-assembly described within Article 3.5 has been applied, the resulting union of these components is defined as “Floor Bodywork”.
3.5.7 Floor Auxiliary Components
Once all parts of Floor Bodywork have been fully defined, the following may be used:
- A single stay per side to act as a rigid support between the Floor Bodywork and the Rear Impact Structure described in Article 13.7. If fitted, this stay must:
- Have its inboard attachment point between XDIF=150 and XDIF=325 on the Rear Impact
- Be of a circular cross section with a diameter of no more than 5mm, with the exception of minimal details at its inboard and outboard attachment points, or for adjustment
- A single device between the Front Floor Structure and the Survival Cell. If fitted, all parts of this device in contact with the external airstream must:
- Be fully within RV-BIB-STAY and be symmetrically arranged about Y=0.
- In any Z-plane contain only one closed
- A single stay per side to act as a support between the Floor Bodywork ahead of XR=0. This stay may be designed to only take load in tension. If fitted, this stay must:
- Be entirely between XR=-850 and XR=0
- Have its outboard attachment on the Floor
- Have its inboard attachment on the entirely sprung part of the
- Be of a circular cross section with a diameter of no more than 5mm, with the exception of minimal details at its inboard and outboard attachment points, or for adjustment
Any parts of these components exposed to the external airstream will be considered part of the Floor Bodywork Group.
3.5.8 Apertures
Once all parts of Floor Bodywork have been fully defined, the following apertures may be added:
- For the sole purpose of cooling auxiliary components, (such as Electrical Components, ) in the region forward of XF=650 and above Z=100. The total area of such apertures must not exceed 500mm2 750mm2 per side of the car.
All areas mentioned in this Article will be measured on the untrimmed Floor Bodywork surface.
3.5.9 Plank Assembly
Below the central surfaces of the Floor Body, the plank assembly must be fitted: consisting of the plank, the skids, and the mountings. The requirements of this article must be satisfied when considering both sides of the car.
The following provisions apply to the plank assembly:
- The upper surface of the plank assembly must lie at Z=0, so that no air can pass between it and the Floor Body or Bib lower
- The plank assembly must be symmetrically arranged about Y=0.
- The forward edge of the plank assembly must lie at XF =430
- The rearmost edge of the plank assembly must lie at XR= -600.
- The thickness of the plank assembly measured normal to the lower surface must be 10mm ± 0.2mm and must be uniform when new. A minimum thickness of 9mm will be accepted due to wear, and conformity to this provision will be checked at the peripheries of the designated
- The plank assembly must have four precisely placed holes the positions of which are given by RV-PLANK. To establish the conformity of the plank assembly after use, its thickness will only be measured at these holes, regardless of whether plank or skid material is
Four additional 10mm diameter holes are permitted provided their sole purpose is to allow access to the bolts which secure the Accident Data Recorder to the survival cell.
The following provisions apply to the plank:
- The geometry of the plank must conform to RV-PLANK with a general manufacturing tolerance of ± 0.5mm and a tolerance on thickness given in (e) above
- The material of the plank is free, but it must be homogeneous with a specific gravity between 1.3 and 1.45, or if pocketed be made from a bonded assembly the upper 0.5mm of which must have a specific gravity of between 1.3 and 1.65 and the remainder, excluding pockets, be made from an homogeneous material with a specific gravity of between 1.3 and 45.
- The plank may comprise no more than three pieces, the forward one of which may not be any less than 900mm in
- In the areas between XF=630 and XC=-800 and behind XC=-400, pocketing of the lower 5mm of the plank from above is permitted. The pocket depth may not reduce the remaining plank material thickness to less than 2mm from either the lowest surface below the reference plane when new or the lower surface of any recesses necessary to fit the skids permitted by items k) to r) of this article. Furthermore, the periphery of any pocket, in any horizontal plane parallel to the reference plane, must be not less than 10mm from either the edges of the plank or any holes or recesses in the plank. In vertical cross section the internal pocket fillet radii must be at least 3mm and in horizontal cross section 10mm. Pockets may only be filled with a material having a specific gravity of less than 0.25.
The following provisions apply to the skids. The lower surface of the plank may be fitted with flush mounted metal skids which:
- May only be fitted in place of plank
- Have a total area no greater than 24000mm² when viewed from
- Are no greater than 4000mm² in area individually when viewed from
- Are fitted in order that their entire lower surfaces are visible from
- Must have a minimum cross sectional thickness of 15mm across its external boundaries in plan
The minimum wall thickness between an internal fixing hole and the external boundaries of the skid must be no less than 7.5mm.
- Must have an upper surface no more than 3mm below the reference
- Must be designed such that they are secured to the car using the fasteners described in items t) to w) of this article and that, when viewed from below, no part of the skid is more than 50mm from the centre line of a fastener which passes through that
- Must be made from Titanium alloy (according to AMS4928 or AMS4911 in annealed condition). Furthermore, they may only be machined from solid and no processes (such as forging, rolling, welding, heat treatment or coating) may be carried out either before or after
- If positioned entirely inboard of Y=120 and between XF= 425 and XF= 625, must be fastened directly to the Front Floor Structure with zero degrees of freedom:
The following provisions apply to the plank and skid mountings. The plank and skids must be fixed to the car using fasteners which:
- Are no smaller than M6 and are made from grade 12.9 or 10.9
- If used to attach a skid to the car, must employ at least 1 fastener per 1,000mm2 of skid area.
- If used to attach a skid to the car, the team must be able to show by calculation that the shanks of the fasteners (which may be no less than 6mm diameter) are the weakest point in the attachment of the skids to the
- May use a load spreading washer if
The total area of the fasteners and any load spreading washers employed with them when viewed from below must be less than 7,500mm2. The area of any single fastener plus its load- spreading washer may not exceed 500mm².
No part of any fastener or load-spreading washer may be more than 8mm below the reference plane. For the avoidance of doubt, the skids referred to in items k) to s) of this article will not be treated as load spreading washers.
3.6 Front Bodywork
3.6.1 Nose
Bodywork declared as “Nose” must:
- Lie within RV-CH-NOSE.
- In any X plane, contain no more than a single closed section which must have no external concave radius of curvature. Between XF= -950 and XA=0, the part of this section which is visible from above, must:
- be a tangent continuous curve
- be tangent to the Z-axis at its outermost extremity
- have no radius of curvature smaller than 45mm at XA=0 which may reduce to a minimum radius of curvature of 20mm forward of XA=0
The provisions of this Article must be satisfied when considering both sides of the car.
- In any Y plane, contain only a single section which, if inboard of Y=150, must be
- Be arranged such that, when viewed from above, no part of RS-CH-NOSE, may be visible.
The following will be exempt from the above:
- The cameras (position 2) and mounting brackets defined in Article 17.7
- When considering both sides of the car, a single aperture for the purpose of driver cooling, such an aperture having a maximum surface area of 1500mm2 when measured on the untrimmed Nose and being situated forward of the section referred to in Article
13.6.1 (a).
- Minimal apertures for front suspension
3.6.2 Forward Chassis
Bodywork declared as “Forward Chassis” must:
- Lie within RV-CH-FRONT and completely enclose RV-CH-FRONT-MIN.
- When considering both sides of the car, at any X plane, not contain any convex radius smaller than 25mm or a concave radius smaller than
Once these requirements have been met, minimal apertures may be applied for access to, and movement of mechanical components.
3.6.3 Mid Chassis
Bodywork declared as “Mid Chassis” must lie within RV-CH-MID.
3.6.4 Mirror Housing
- The bodywork declared as “Mirror Body” must lie within RV-MIR-HOU.
- The bodywork defined as “Mirror Inner Stay” must connect the Mirror Body to the Mid Chassis and must:
- Lie between two X-Planes, located at the forward and rearward extremities of the inboard face of RV-MIR-HOU
- Not lie above a plane parallel to and offset upwards by 25mm from the lower face of RV-MIR-HOU or below Z=550
- Lie inboard of the inboard face of RV-MIR-HOU
- Form no more than a single section when intersected by any Z-plane or Y-Plane
- The Mirror Body may be connected to the Sidepod by bodywork declared as “Mirror Rear Stay”. If present, this bodywork must:
- Lie between Y=440 and Y=630.
- Lie behind a plane lying on the forward face of RV-MIR-HOU
- When cut by any X-Plane, form a single section measuring no more than 50mm in Z and no more than 10mm in
- Lie forward of the plane XF=1300 and lie between two Z-Planes at Z=400 and Z=720.
- Once the Mirror Inner Stay and Mirror Rear Stay (if present) are fully defined, they must be trimmed to the Mirror Body to produce a single volume. A fillet with radius of no more than 10mm may be applied to the intersections between these volumes. The resulting volume is defined as Mirror
- Once fully defined, the Mirror Housing must be trimmed to all of the following bodywork components it connects to: Mid Chassis, Sidepod and the fillet defined in Article 3.11.1. A fillet with radius of no more than 10mm may be applied to the intersections between the Mirror Housing and these
3.6.5 Front Bodywork Group
Once the components defined in Articles 3.6.1 to 3.6.4 have been constructed in accordance to the provisions of those Articles, and any subsequent operation of sub-assembly described within those Articles has been applied, the resulting union of these components is defined as “Front Bodywork”.
3.6.6 Continuity
Once all parts of the Front Bodywork have been fully defined, the external surfaces at the boundaries between adjacent sections of the Nose, Forward Chassis and Mid Chassis bodywork, must maintain both continuity and tangency in any Y or Z plane.
3.7 Rear Bodywork
3.7.1 Sidepod
Bodywork declared as “Sidepod” must:
- Lie within RV-RBW-SPOD.
- Form no more than two curves on its surface when intersected by any X or Y plane, each of which must be tangent continuous and open. Furthermore:
- Assessed on any X plane, any such curve that is wholly or partially visible when viewed from the side of the car, is subject to the following requirements:
Parts of this curve that are visible from the car centre plane (viewed parallel to the Y-axis) and not visible from the side may contain no concave radius of curvature (as defined by Article 3.1.4) smaller than 50mm.
All other parts of this curve may contain no concave radius of curvature smaller than 200mm.
- Assessed on any Y plane, whenever two such curves are visible when viewed from the front of the car, no part of either curve may have a concave radius of curvature smaller than
- Compliance with (i) and (ii) is not required within a single 50mm diameter sphere defined by the
- In any Z plane, any cross section of bodywork must form a single curve on its surface which must be tangent continuous and
3.7.2 Coke Panel
Bodywork declared as “Coke Panel” must:
- Lie within RV-RBW-COKE.
- At no point be less than 50mm distant to RV-FLOOR-EDGE.
- Be arranged such that, when viewed from the side, no part of RS-RBW-EC that lies within RV-RBW-COKE may be
3.7.3 Engine Cover
Bodywork declared as “Engine Cover” must:
- Lie within RV-RBW-EC.
- Be arranged such that when viewed from the side, no part of RS-RBW-EC that lies within RV-RBW-EC may be
3.7.4 Coke Panel and Engine Cover Shape
On each side of the car, the combined external Coke Panel and Engine Cover surfaces must:
- On any X section, form one tangent continuous curve. Furthermore:
- Outboard of Y=25 the radius of curvature of any such section must not be less than 75mm if convex, or 50mm if concave, with the exception of a rectangular region bounded in plan view by (XC=20, 125) and (XC=150, 375) where the radius of curvature must not be less than 25mm and within a 20mm offset from the lower side impact structure defined in article 13.5.1 where the radius of curvature must not be less than
- Between Y=5 and Y=25 the radius of curvature of any such section must not be less than
- Not contain any apertures ahead of XR= -55, other than those permitted in Article 7.6.
- Not contain any surface parallel to a X plane ahead of XR= -55.
- Rearward of XR = -300, and below Z=350, and prior to the addition of any apertures, the X component of any normal to the external surface of bodywork visible from the side must not be
The cameras (position 3) and mounting brackets defined in Article 8.17.8 will be exempt from the restrictions of this Article.
3.7.5 Bodywork Blister
Once the Rear Bodywork surfaces are fully defined in accordance with Articles 3.7.1 to 3.7.4, a single Bodywork Blister may be added per side, which must:
- Exist entirely between XR =-50 and XR = -600, below Z=550 and inboard of Y=250.
- Lie entirely between the Rear Bodywork surfaces and a 50mm external offset of
- In side-view, lie entirely within an axis-aligned rectangle which is 350mm long and 120mm
- Intersect the Rear Bodywork surfaces around its entire
- Only comprise convex curvature, with a minimum radius of
- At no point on its surface have a normal with a negative X component that subtends an angle greater than 20deg to an X
Once the Bodywork Blister surfaces are fully defined, the Bodywork Blister and Rear Bodywork must be trimmed to each other, such that no overlapping surfaces remain. A fillet radius, no smaller than 20mm, must be applied along the intersection between these surfaces.
3.7.6 Apertures
Once the Rear Bodywork surfaces are fully defined in accordance with Articles 3.7.1 to 3.7.5, the following apertures may be added:
- For the purpose of allowing suspension members and their fairings and driveshafts to protrude through the bodywork and provided that the result of adding the aperture does not subvert the intention of regulation 3.7.4, a single aperture may be added for each suspension member and driveshaft. No such aperture may have an area greater than 12,000mm2. No point on an aperture may be more than 200mm from any other point on the aperture. Individual apertures may adjoin or overlap each other. At the legality ride height defined in Article 10.1.4, the aperture must enclose the suspension member, including its fairing, or driveshaft for parts forward of XR= -55.
- For the sole purpose of allowing cooling flow exits, apertures may be added provided they lie within RV-RBW-APERTURE. The total area (per side of the car) of such apertures may be no greater than 150,000mm2. Furthermore, any apertures added must be arranged such that, when viewed from above, no part of RS-RBW-APERTURE may be visible through the aperture and any underlying part of the car exposed by application of an aperture must lie no further than 50mm normal to the untrimmed surface. For the avoidance of doubt, no part of the car exposed by application of an aperture may lie external to the untrimmed
- For the sole purpose of allowing cooling flow exits, apertures may be added inboard of Y= 25. The total area of such apertures may not be greater than 30,000mm2 per side of the
- For the sole purpose of cooling auxiliary components, (such as Electrical Components, ), apertures may be added forward of XF=1300 or below Z=100. The total area of such apertures may not exceed 5,000mm2 per side of the car.
All areas mentioned in this Article will be measured on the untrimmed Rear Bodywork surface.
3.7.7 Rear Bodywork Group
Once the components defined in Articles 3.7.1 to 3.7.6 have been constructed in accordance to the provisions of those Articles, and any subsequent operation of sub-assembly described within those Articles has been applied, the resulting union of these components is defined as “Rear Bodywork”.
3.7.8 Continuity
Once the Front and Rear Bodywork are fully defined, the external surfaces at the boundaries between adjacent sections of the Front Bodywork, Sidepod, Coke Panel, Engine Cover, and Bodywork Blister parts, must maintain continuity in any X, Y or Z plane.
Furthermore, the external surfaces at the boundaries between adjacent sections of the Sidepod, Coke Panel, Engine Cover, and Bodywork Blister parts, must also maintain tangency in any X, Y or Z plane.
3.8 Tail and Exhaust Tailpipe
3.8.1 Tail
Bodywork declared as “Tail” must:
- Lie within RV-TAIL.
- In any X-plane rearwards of XR=440, contain only a single closed section, when considering both sides of the
- Not be visible from below forward of XR=440 and with the Floor Body present. The following will be exempt from the above:
- When considering both sides of the car, a single aperture for the purpose of cooling electrical components. Any such an aperture must have an area no greater than 250mm2 when measured on the untrimmed surface of Tail and must be behind XR=450.
3.8.2 Exhaust Tailpipe
Bodywork declared as “Exhaust Tailpipe” must:
- Lie within the union of RV-TAIL and RV-TAIL-EXH. Furthermore, when considering both sides of the car:
- Over its last 150mm, the Exhaust Tailpipe must comprise of a single tailpipe and its minimal
- Over its last 450mm:
- The turbine tailpipe through which all the turbine exit fluids pass must have a circular internal cross-section of a constant diameter between 100mm and 130mm.
- Any wastegate tailpipe(s) through which all the wastegate exit fluids pass must have an internal cross section less than 1500mm2, and all external surfaces must have minimal aerodynamic effect on the external air
- The inside of the Exhaust Tailpipe must remain unobstructed and in full compliance with the provisions of this Article after the Final Assembly of all bodywork
Minimal exceptions, solely for the purpose of permitting the wastegate tailpipe(s) to join the turbine tailpipe, are allowed over an axial length of up to 100mm and more than 150mm from the Exhaust Tailpipe exit.
- Over its last 150mm, the Exhaust Tailpipe must have an internal surface which is a right circular cylinder, with an axis that lies on Y=0 and forms an angle between 0deg and 5deg to the X-axis (tail up).
- The Exhaust Tailpipe must have an exit whose entire circumference lies between XR=550 and XR=565 and above Z=
- The Exhaust Tailpipe must have a thin wall, of constant thickness, with the exception of minimal, external, local
3.9 Front Wing (FW)
3.9.1 Front Wing Profiles
Bodywork declared as “Front Wing Profiles” must lie within RV-FW-PROFILES. In any Y plane, the following conditions apply:
- There must be no more than four closed
- No closed section may contain any concave radius of curvature less than 50mm
- The distance between adjacent sections must lie between 5mm and 15mm at their closest
- The rearmost point of every closed section must be visible when viewed from
- With the exception of the rearmost closed section, the rearmost point of every closed section must not be visible when viewed from
- Assessing each closed section independently, the part of any closed section visible when viewed from below may contain no concave radius of
- Within 40mm of the rearward-most point of each closed section a line tangent to any part of the section visible from below must have a positive slope. The slope of this line will be considered in the Y-plane.
- Within 40mm of the rearward-most point of each closed section, no part of the section visible from above may be more than 8mm 10mm distant from the section visible from below, if outboard of Y=500, or 15mm if inboard of Y=500.
- Inboard of Y=300, the forward-most two closed sections, must have a maximum thickness of at least 25mm when measured in the Z
Furthermore, when considering the entire profiles, the following conditions apply:
- The normal to any point of the profiles surface must not subtend an angle greater than 25° to a vertical plane that is normal to RS-FW-SECTION for the forward most two profiles and 30° for any other
- The rearward most point of every closed section, when projected in Z on to the reference plane, must produce a single tangent continuous curve with no radius of curvature smaller than
- The Front Wing Profiles must be arranged such that, when viewed from below, no part of RS-FW-PROFILES may be
Once the Front Wing Profiles are fully defined Gurneys of up to 10mm may be fitted to the trailing edge of the upper surface of the rearmost section. These Gurneys are considered to be part of the Front Wing Profiles and must satisfy the provisions of this Article with the exception of sections (b) and (h) and, for the inner extremity of the innermost Gurney and outer extremity of the outermost Gurney, section (j).
3.9.2 Front Wing Endplate Body
Bodywork declared as “Front Wing Endplate Body” must lie within RV-FW-EP and be constructed by the following process:
- A virtual surface must first be defined, which must:
- Produce no more than one curve when intersected with any Z plane. At no point along this curve may a line tangent to it subtend an angle greater than 10° to the X-Axis.
- Produce no more than one curve when intersected with any X plane. At no point along this curve may a line tangent to it subtend an angle greater than 10° to the Z-Axis.
- Once the virtual surface has been defined, the Front Wing Endplate Body must:
- Fully enclose the entire virtual
- Be no more than 10mm distant from the virtual surface at any point. Regions further than 150mm in X from its forward most point on the same Z-plane, must be no more than 6mm distant from the virtual surface at any
- Once fully defined, the Front Wing Endplate Body must be arranged such that when viewed from the side, no part of RS-FWEP-BODY may be
- With the exception of regions of the Front Wing Endplate Body surface that are not in contact with the external air stream after the Front Wing Assembly is complete, its complete and final surface must be tangent continuous and any concave radius of curvature must be greater than
3.9.3 Front Wing Tip
Bodywork declared as “Front Wing Tip” must:
- Lie within the RV-FW-TIP.
- Be a single volume with no apertures. Furthermore:
- The following must apply to the intersection between regions of the Front Wing Tip below Z=170 and any plane that contains the X-aligned axis [Y,Z] = [900, 170]:
- There must be no more than four closed
- No closed section may contain any concave radius of curvature less than
- The distance between adjacent sections must be no more than 15mm at their closest
- For any two adjacent sections, the trailing edge of the forward section must be at a greater distance from the X-aligned axis than the leading edge of the rear section.
- When measured in the X-direction, each section must be larger than 50mm and no more than 30mm of this may overlap, in X, any other section in the same plane.
- The intersection between the Front Wing Tip and any Z plane between Z=170 and Z=180 must produce no more than four closed sections and above Z=180 must produce no more than one closed
- For any section described in (c) and (d), the forward-most point and the rearward-most point, measured in X, must each be situated between a pair of planes from a set defined as follows:
- All planes must be vertical and oriented within the angular range defined by the acute angle between an X-plane and RS-FW-SECTION.
- Each pair must consist of two parallel planes no more than 35mm apart. This is except for the pairs whose intersection with RV-FW-TIP is furthest forward and furthest rearward, which must be no more than 50mm
- The total number of pairs of planes must be equal to one plus the number of closed sections produced by the intersection of the FW Tip and the plane Y=900.
- No two planes may be coincident with each other and no part of RV-FW-TIP may lie within more than one of these pairs of
- With the exception of regions of the Front Wing Tip surface that are not in contact with the external air stream as a result of assembly with the Front Wing Profiles and Front
Wing Endplate, curves produced by the intersection of the Front Wing Tip with any X plane must:
- Be tangent-continuous and not contain any radius less than
- Not contain any concave radius less than 1000mm if formed from any surface that is visible from the side or below. This is except for regions of the curve above Z=170, where a minimum concave radius of 200mm will be
- Compliance with (f) is not required in the following regions:
- within 35mm of up to THREE “Junction Points”, which must lie above Z= 160, and not be closer than 50mm to each other. Surfaces exempt from (f) within these regions must lie above Z=150 and inboard of a 3mm external offset of the outboard face of the Front Wing Tip at Z=200 when viewed from
- within 10mm of the forward-most point of each individual closed section described in (c) and (d).
- within 3mm of the rearward-most point of each individual closed section described in (c) and (d), within 6mm if this section is the rearward-most section, and within 10mm for the rearward-most section if the point is above Z=170.
3.9.4 Front Wing Diveplane
Bodywork must be declared as “Front Wing Diveplane”, lie within RV-FW-DP and be constructed by the following process:
- A virtual surface must first be defined, which must:
- Produce no more than one curve when intersected with any Y plane, the rearward most point of this curve must lie at least 75mm above its forwards most
- Produce no more than one curve when intersected with any X plane, at no point along this curve may a line tangent to it subtend an angle greater than 25° to the Y-Axis.
- Once the virtual surface has been defined, the Front Wing Diveplane must:
- Fully enclose the entire virtual
- Be no more than 6mm distant from the virtual surface at any
- Once fully defined, the Front Wing Diveplane must be arranged such that when viewed from above, no part of RS-FW-DP may be
- Its complete and final surface must be tangent continuous and any concave radius of curvature must be greater than
3.9.5 Front Wing Endplate
Once the Front Wing Diveplane and Front Wing Endplate Body are fully defined, the Front Wing Diveplane must be trimmed to the Front Wing Endplate Body to create one unified volume with no remaining overlapping surfaces. Any Front Wing Diveplane bodywork remaining inboard of the Front Wing Endplate Body must be discarded. A fillet radius, no greater than 10mm, may be applied along the intersection between these volumes.
Furthermore, once the trim is complete:
- Any section of the unified volume taken through an X plane should contain only one closed
- When viewed from the car centre-plane, no part of the Front Wing Diveplane may be visible.
- In order to prevent tire damage to other cars, the complete Front Wing Endplate must be at least 10mm thick (being the minimum distance when measured normal to the surface in any direction). When assessing this thickness, adjoining parts of the Front Wing Tip may also be considered. Furthermore, with the exception of parts of the Front Wing Endplate that lie on the shared boundary of RV-FW-EP and RV-FW-TIP a 5mm edge radius must be applied to all
3.9.6 Front Wing Assembly
Once the Front Wing Endplate, Front Wing Profiles and Front Wing Tip are fully defined, they must be trimmed to each other to create one unified volume with no remaining overlapping surfaces. Furthermore, the external surfaces at the boundaries between adjacent sections of the Front Wing Endplate, Front Wing Profiles and Front Wing Tip, must maintain both continuity and tangency in any X, Y, or Z plane.
3.9.7 Adjustability of Front Wing
Once the Front Wing Assembly has been defined in accordance with Article 3.9.6, a continuous portion of either the rearmost or the two rearmost profiles (including any Gurney rigidly attached to it) may be adjustable for the sole purpose of trimming front wing aerodynamic load. This adjustable part of the Front Wing Profiles will be called the FW Flap.
The axis of rotation of the adjustable part of the wing must:
- Pass through points A and B where:
- Point A lies within the volume of the FW Flap, no more than 25mm from its forward most point at this Y and between Y=200 and Y=400.
- Point B lies within the volume of FW Flap, no more than 25mm from its forward most point at this Y and between Y=825 and Y=850.
- Be no more than 70mm from the FW Flap at any point between points A and
- Once the axis of rotation AB has been defined, two surfaces of revolution must be defined. These surfaces must:
- Have the axis AB as their axis of revolution, and respectively pass through points A (one surface) or B (the other surface).
- Extend over the complete chord of the FW Flap, thus clearly defining its boundaries in relation to the non-adjustable part of the Front Wing
- Over their intersection with the FW Flap at its original design position (defined in accordance to Article 3.9.1), have a normal which does not subtend an angle greater than 30deg to the Y
Furthermore:
- Compared to the original position of these profiles (as defined in accordance with Article 3.9.1), adjustment may only permit an increase of incidence of the slope defined in Article 3.9.1.g, and the maximum deviation for any point of these profiles from its original position must not exceed
- Minimal exceptions to the geometrical criteria of Article 3.9.1 for the wing profiles may be made in the junction between the adjustable and non-adjustable parts, in order to ensure the necessary level of sealing. Such parts must lie within 3mm from one of the two surfaces of revolution and their maximum size must be the minimum necessary amount required to achieve a 20mm overlap between the adjustable and the
non-adjustable parts of the profiles over the whole range of movement In the case where the trailing edge of the rearmost element is trimmed, any such parts with minimal exceptions can remain untrimmed, provided that the remaining parts extend no more than 20mm behind the trimmed trailing edge.
For the avoidance of doubt, the adjustment permitted under this Article is only allowed when the car is stationary and by the use of a tool, and in accordance with the Sporting Regulations.
Furthermore, any such variation of incidence must maintain compliance with all of the bodywork regulations, with the exception of Article 3.9.1.
3.9.8 Front Wing Auxiliary Components
The following components will be permitted in addition to the Front Wing Assembly:
- Up to three brackets which define the pivot axis of the FW Flap and allow the necessary movement. Each bracket must:
- be in its entirety within 40mm of the FW Flap, per side of the car, over the whole range of
- be no more than 5mm thick and lie within two parallel planes no more than 10mm
- have no dimension that exceeds 80mm. Furthermore, when projected in X on to an X-plane, the area of each separator must be less than 750 mm2.
Once the above requirements have been met, a fillet radius no greater than 4mm will be permitted where these brackets join the two profiles.
- Up to eight slot gap separator brackets, per side of the car, which provide a structural connection between consecutive FW Profiles. Each bracket must:
- be in its entirety within 40mm of both of the two profiles that it supports in relation to each
- be no more than 6mm thick and lie within two parallel planes no more than 10mm
- have no dimension that exceeds 70mm. Furthermore, when projected in X on to an X-plane, the area of each separator must be less than 750 mm2.
Once the above requirements have been met, a fillet radius no greater than 4mm will be permitted where these brackets join the two profiles.
- A mechanism with or without a fairing to contain it for the angle adjustment of part of the FW Flap, as defined in Article 3.9.7. This mechanism and fairing must fit within a cuboid of which is 25mm wide, 60mm long and 65mm high. This cuboid may have a free orientation in space, but must intersect both the stationary and the adjustable part of the profiles for the entire range of
- A fairing that contains a single tire temperature sensor. The entire fairing and sensor must:
- fit in the union between two volumes, a cuboid which is 15mm wide, 60mm long and 50mm high and a circular cylinder which has a base diameter of 30mm and a height of 60mm. The axis of the cylinder must coincide with the major axis of the one of the 15mm x 60mm faces of the
- be symmetrical about a plane which is parallel to the 50mm x 60mm faces of the cuboid, and
- intersect either the Front Wing Profiles defined in Article 3.9.1 or the Front Wing Endplate Body defined in Article 3.9.2. A fillet radius no greater than 5mm will be permitted along this
Furthermore, all the components listed above must be arranged such that they are not visible from below and do not lie outboard of the virtual surface defined in 3.9.2.a.
Should there be a requirement for any additional component to be added, the Competitor must write specifically to the FIA with an explanation, design, and calculated aerodynamic effect, in order to get approval. Such a communication will be circulated to rival Competitors if deemed to cover a new aspect that had previously not been considered.
3.9.9 Front Wing Bodywork Group
Once the components defined in Articles 3.9.1 to 3.9.8 have been constructed in accordance to the provisions of those Articles, and any subsequent operation of sub-assembly described within those Articles has been applied, the resulting union of these components is defined as “Front Wing Bodywork”.
3.10 Rear Wing
3.10.1 Rear Wing Profiles
Bodywork declared as “Rear Wing Profiles” must:
- Lie within RV-RW-PROFILES.
- In any Y plane:
- Contain exactly two
- The rearmost section, which will be known as the “RW Flap”, must have a chord smaller than the chord of the adjacent
- With the exception of minimal modifications to permit attachment of the actuator system described in 3.10.10 to the RW Flap, the sections may not contain any concave radius of curvature smaller than 100mm
- The distance between the two sections must lie between 10mm and 15mm at their closest
Furthermore:
- Outboard of Y100, the normal to any point of the profiles surface must not subtend an angle greater than 20° to a Y
- Once the RW Flap is fully defined, a Gurney of up to 20mm may be fitted to the trailing edge. This Gurney is considered to be part of the Rear Wing Profiles and must satisfy the provisions of this Article with the exception of sections b (iii) and (c).
3.10.2 Pylons
Bodywork declared as “Rear Wing Pylon” must:
- Lie within RV-RW-PYLON.
- On any Z plane, when considering both sides of the car, only contain no more than two closed symmetrical sections with a maximum total area of 5000mm2. This does not apply if the complete section lies within 30mm of the Exhaust Tailpipe defined in Article
3.8.2. For any complete closed section outside of RV-TAIL-EXH, the thickness of each section may not exceed 25mm when measured in the Y direction.
Once the Rear Wing Pylon and Rear Wing Profiles are fully defined the Rear Wing Pylon must be trimmed to the Rear Wing Profiles such that no overlapping surfaces remain. A fillet radius, up to 10mm, may be applied along the intersections between these surfaces.
3.10.3 Rear Wing Beam
Bodywork must be declared as “Rear Wing Beam” and must:
- Lie within RV-RW-BEAM.
- At no point be less than 10mm distant to the Exhaust Tailpipe once fully defined in accordance to Article 8.2.
- In any Y plane:
- Contain no more than two
- The section may not contain any concave radius of curvature smaller than 50mm Furthermore:
- The Rear Wing Beam must be arranged such that when viewed from above no more than 80,000mm2 of RS-RW-BEAM may be visible per side of the
- Outboard of Y=175, the normal at any point on the profiles’ surface must not subtend an angle greater than 15° to a Y plane. Inboard of Y=175mm, the normal at any point on the profiles surface must not subtend an angle greater than 60° to a Y
Once the profiles have been fully defined:
- A Gurney of up to 20mm may be fitted to the trailing edge of the rearward most profile. This Gurney is considered to be part of the Rear Wing Beam and must satisfy the provisions of this Article with the exception of sections c (ii) and (e).
- Provided two closed sections are present as specified in (c), up to two slot gap separator brackets, per side of the car, will be permitted. These brackets must:
- Be in their entirety within 30mm of both of the two profiles they support in relation to each
- Be no more than 6mm thick. A fillet radius no greater than 2mm will be permitted where these brackets join the two
- Have no dimension that exceeds 60mm
- Not be visible from below with the Rear Wing Beam Profiles present
3.10.4 Rear Wing Endplate Body
Bodywork declared as “Rear Wing Endplate Body” must:
- Lie within RV-RWEP-BODY.
- Be a single volume with no
- In any X or Z plane contain only one closed section. Furthermore, any such section, on any X or Z plane, must not contain an external concave radius of curvature smaller than 100mm.
3.10.5 Rear Wing Tip
Bodywork declared as “Rear Wing Tip” must:
- Lie within the RV-RW-TIP.
- Be a single volume with no apertures. Furthermore:
- The following must apply to the intersection between regions of the Rear Wing Tip above Z=670 and any plane that contains the X-aligned axis [Y, Z] = [480, 670]
- There must be no more than two closed
- The distance between adjacent sections must be no more than 15mm at their closest
- When measured in the X-direction, each individual section must be larger than 100mm and no more than 40mm of the complete intersection may contain more than two points with the same X-coordinate.
- The intersection between the Rear Wing Tip and any Z plane between Z=660mm and Z= 670mm must produce a single closed
- Its complete surface must be tangent continuous, and any concave radius of curvature must be greater than 20mm. Furthermore, any surface visible from the side or above must not contain any concave radius of curvature smaller than
- Curves produced by the intersection of the Rear Wing Tip with any X plane must:
- Be tangent continuous and not contain any radius less than 20mm forwards of XR=550.
- Not contain any concave radius less than 1000mm if formed from any surface that is visible from the side or any surface forwards of XR=550 that is visible from
The sole purpose of the external surfaces of the Rear Wing Tip is to create a smooth transition, with no discontinuities, between the Rear Wing Profiles and the Rear Wing Endplate Body. Provided this purpose is observed, and the following are only used at the leading and trailing edges of the sections used to create this transition:
- Compliance with Section (f) of this Article is not required in the following regions of the Rear Wing Tip:
- within 10mm of the forward-most point of each individual closed section described in (c) and (d).
- within 3mm of the rearward-most point of each individual closed section described in (c) and (d).
- Compliance with Sections (e) and (f) of this Article are not required in the following regions of the Rear Wing Tip:
- Regions not in contact with the external air stream after the Rear Wing Assembly is
- Within 30mm of a single “Junction Point”. This Junction Point must lie above Z= 670.
3.10.6 Rear Wing Separators
Once the Rear Wing Profiles and the Rear Wing Tip are fully defined, the two closed sections described Articles 3.10.1.b and 3.10.5.c must be bridged by three pairs of rigid impervious supports. One pair of supports must be located at Y=0 with the remaining supports arranged symmetrically about the car centre plane and lying in their entirety between Y=+/-470 and Y=+/-490. These pairs of supports must be designed and arranged such that the two closed sections and the relationship between them can only change whilst the car is in motion in accordance to Article 3.10.10. They must:
- With the exception of minimal local changes where the two sections are adjacent to each other and with the rearmost element in the closed position, have an inner profile that is coincident to the section they are fixed to, an outer profile that is an offset of the inner profile of no more than 15mm and may not incorporate any radius smaller than 10mm in sideview (‘gurney’ type trim tabs may however be fitted between the supports).
- Be aligned as a pair so as to provide a bearing across at least 40mm2 when the distance between the two sections is at its closest
- Not be recessed into the Rear Wing Profiles or Rear Wing Tip (where a recess is defined as a reduction in section at a rate greater than 45° with respect to the Y-axis).
- Be arranged so that any curvature occurs only in a horizontal plane (other than when this bodywork is adjusted in accordance with Article 10.10).
- Not be visible from below when the Rear Wing Profiles and Rear Wing Tip are
- Have no dimension that exceeds 150mm when considering the forward most part of the
- Have no dimension that exceeds 30mm when considering the rearward most part of the
- Be between 2mm and 6mm
- Be rigidly fixed to their respective section. Where they are fixed, a fillet radius of no greater than 4mm will be permitted between the support and the Rear Wing Profiles or the Rear Wing
- Be constructed from a material with a modulus greater than 50
3.10.7 Rear Wing Endplate
Once the Rear Wing Endplate Body and Rear Wing Tip are fully defined they must be joined to create one unified volume with no remaining overlapping surfaces. The resultant volume, known as the Rear Wing Endplate must be arranged such that, when viewed from the side of the car, no part of RS-RW-RWEP, may be visible. Furthermore, the external surfaces at the boundaries between adjacent sections of the Rear Wing Endplate Body and Rear Wing Tip must maintain both continuity and tangency in any X, Y or Z plane.
3.10.8 Continuity
Once the Rear Wing Endplate is fully defined, the external surfaces at the boundaries between adjacent sections of the Rear Wing Endplate, and Rear Wing Profiles must maintain both continuity and tangency in any X, Y or Z plane.
3.10.9 Rear Wing Beam Assembly
Once the Rear Wing Endplate and Rear Wing Beam are fully defined the Rear Wing Beam must be trimmed to the Rear Wing Endplate such that no overlapping surfaces remain. Any Rear Wing Beam bodywork remaining outboard of the Rear Wing Endplate must be discarded. A fillet radius, no greater than 10mm, may be applied along the intersections between these volumes. Furthermore, once the trim is complete, when viewed from the side, no part of the Rear Wing Beam may be visible.
3.10.10 Drag Reduction System (DRS)
The entire RW Flap described in Article 3.10.1, including any gurney if fitted, part of the rearward most section from any regions of the Rear Wing Tip described in Article 3.10.5 where there are exactly two sections in an intersection with any plane that contains the X- aligned axis [Y,Z]= [480, 670], and the portions of the Rear Wing Separators defined in 3.10.6 that are attached to these components, may be rotated about a fixed axis whilst the car is in motion. All bodywork to be rotated shall be known as “DRS Bodywork”
Furthermore:
- No part of the “DRS Bodywork” may lie outboard of Y=490.
- The axis of rotation of the RW Flap must be fixed and located no more than 20mm below the upper extremity and no more than 20mm forward of the rear extremity of RV-RW-PROFILES at all
- There must be no relative movement between the constituent parts of the DRS Bodywork.
- Any such variation of incidence maintains compliance with all of the bodywork regulations with the exception of Article 3.10.1 and 10.5.
- It cannot be used to change the geometry of any duct, either directly or indirectly, other than the change to the distance between adjacent sections permitted by Article 3.10.1 and 10.5.
- The design is such that failure of the system will result in the uppermost closed section returning to the normal high incidence
- Any alteration of the incidence of the uppermost closed section may only be commanded by direct driver input and controlled using the control electronics specified in Article 3.
- At any Y plane, the distance between the two sections of the Rear Wing Profiles at their closest position must lie between 10mm and
In order to achieve the above adjustment, the actuator mechanism and any associated minimal fairings must lie inboard of Y=25, below Z=940 and not extend beyond
RV-RW-PROFILES in the forward or rearward direction, when viewed from above. Furthermore, any additional minimal bodywork associated with the adjustment of the DRS Bodywork must be located outboard of Y= 465 and in side-view be below the top surface of RV-RW-PROFILES, must not be visible from below and must fit within a cuboid which is 30mm wide, 60mm long and 30mm high. This cuboid may have a free orientation in space, but its width must be aligned with the axis of rotation of the RW flap.
3.10.11 Rear Wing Bodywork Group
Once the components defined in Articles 3.10.1 to 3.10.10 have been constructed in accordance to the provisions of those Articles, and any subsequent operation of
sub-assembly described within those Articles has been applied, the resulting union of these components is defined as “Rear Wing Bodywork”.
3.11 Final Assembly
This Article gives additional information on the junction between adjacent bodywork groups defined in Articles 3.5 to 3.10.
3.11.1 Front Bodywork to Rear Bodywork
Once both the complete Front Bodywork and the Rear Bodywork are fully defined, the Front Bodywork and the Rear Bodywork must be trimmed to each other, such that no overlapping surfaces remain. A maximum fillet radius, no greater than 50mm, may be applied along the intersections between these surfaces.
3.11.2 Front and Rear Bodywork Assembly to Floor Bodywork
Once both the complete Front and Rear Bodywork assembly defined in Article 3.11.1 and the Floor Bodywork are fully defined, the Front and Rear Bodywork assembly and the Floor Bodywork must be trimmed to each other, such that no overlapping surfaces remain.
Additionally, before the trimming is applied, any Mid Chassis or Rear Bodywork remaining below the Floor Bodywork must be discarded and the intersection formed by any remaining surfaces and the Floor Bodywork must produce no more than one curve. A maximum fillet radius, no greater than 50mm, may be applied along the intersection between these surfaces. Any such fillet must be at least 1mm distant from RV-FLOOR-EDGE. Furthermore, once all surfaces are trimmed and filleted, no part of the Mid Chassis, Rear Bodywork, fillet between the Rear Bodywork and the Floor Bodywork, or fillet between the Mid Chassis and the Floor Bodywork, may be visible from below.
Once the Front and Rear Bodywork has been assembled to the Floor Bodywork, up to two apertures may be added on each side of the car for the sole purpose of giving tire temperature sensors visibility of the tires, one for the front tire and one for the rear tire. If present, each individual aperture must have an area no greater than 1500mm2 when measured on the assembled, untrimmed, surface.
3.11.3 Tail to Floor and Bodywork Assembly
Once both the complete Tail, and the Floor and Bodywork Assembly created in 3.11.2 are fully defined, the Tail, and the Floor and Bodywork Assembly must be trimmed to each other, such that no overlapping surfaces remain. A maximum fillet radius, no greater than 50mm, may be applied along the intersections between these surfaces.
3.11.4 Front Wing Bodywork to Nose
Once both the complete Front Wing Bodywork and the assembly referred to Article 3.11.2 are fully defined, the Front Wing Bodywork, ignoring any Gurneys, and the Nose must be trimmed to each other, such that no overlapping surfaces remain. A fillet radius, up to 25mm, may be applied along the intersections between these surfaces. Once all surfaces, ignoring any Gurneys, are trimmed and filleted, only Nose bodywork and fillet and no part of the Front Wing Bodywork, ignoring any Gurneys, may remain directly above RS-CH-NOSE.
3.11.5 Rear Wing Bodywork to Tail
Once both the complete Rear Wing Bodywork and the Tail are fully defined, the Rear Wing Bodywork and the Tail Bodywork must be trimmed to each other, such that no overlapping surfaces remain. A fillet radius, up to 10mm, may be applied along the intersections between these surfaces.
3.12 Bodywork not defined in Articles 3.5 to 3.11
In addition to the bodywork defined and regulated by Articles 3.5 to 3.11, the following components are permitted:
- A transparent windscreen may be fixed to the forward face of the cockpit opening and may extend above RV-CH-MID.
- Antennae and pitot tubes may be mounted on the upper surface of the survival cell ahead of the cockpit opening and may extend above RV-BODY-FRONT.
- The following fairings may be attached to the secondary roll structure defined in Article 12.4.2, or the cameras defined in Articles 8.10.3 and 17.6:
- A fairing bonded to the secondary roll structure, which:
- Must lie entirely within a 20mm offset from the secondary roll structure or high-speed camera, above Z=695mm and outside of RV-COCKPIT-HELMET.
- Must not have any part with a convex radius of less than 2mm
- An additional fairing around the secondary roll structure forward mounting and the camera defined in Article 8.17.6, which:
- Must lie in a volume defined by an axis-aligned cuboid, which has one interior diagonal defined by points [XC= -1066, -25, 600] and [XC= -835, 25, 705].
- May be joined to the Front Bodywork with a fillet radius of no greater than 10mm.
- A fairing bonded to the secondary roll structure, which:
- Ducts (as specified in Article 3.1.1) and primary heat exchangers provided they are not visible when viewed from the outside of the car, at any angle perpendicular to the X-axis. This is assessed with the bodywork defined in Articles 3.5 to 3.11 present but prior to the application of apertures permitted in Articles 3.5.8, 3.6.1.f, and 7.6.
- A slip sensor and its minimal fairings may be mounted underneath the Forward Chassis provided it lies entirely within 25mm of the car centre plane, above Z=120 and in the region 50 < XF < 450. The external surface of the combined slip sensor and fairings must form a single curve when intersected by any Z
3.13 Wheel bodywork
3.13.1 General principles
Geometry declared as “Front Wheel Bodywork” and “Rear Wheel Bodywork” must comprise of all the components described in Articles 3.13.2 to 3.13.7.
When referred to individually, these components will have the words “Front” or “Rear” added to the component name.
Any criteria of visibility will assume that the sprung mass, the suspension, the RS-FWH-DRUM assembly, the drum to wheel seals and the complete wheels have been removed, and will be considered in the orthogonal frame of reference of the wheel (XW, YW, ZW).
With the exception of the Wheel Covers and minimal flexible parts for the sole purpose of allowing an aerodynamic seal to be maintained to the suspension members and wheels, the Wheel Bodywork must:
- Be rigid and rigidly secured to the suspension uprights (rigidly secured means not having any degree of freedom).
- Not be rigidly secured to the suspension
3.13.2 Drum
The Front and Rear Drums must be made respectively to the geometry defined by
RS-FWH-DRUM and RS-RWH-DRUM.
For each drum, a circumferential, continuous (around an arc of 360°), and uniform aerodynamic seal must be fitted in the outboard of the two annotated volumes, in order to prevent any significant aerodynamic or heat transfer flow between the drum and the axle.
An optional aerodynamic seal may be fitted in the inboard of the two annotated volumes between the drum and the wheel rim. If fitted, this seal must be circumferential, continuous (around an arc of 360°), and uniform.
Notwithstanding this specification, the following modifications will be permitted inboard of YW= -5:
- Apertures where suspension members or suspension fairings intersect the surface of the Drum. These apertures must be minimal in size in order to permit the full articulation of the suspension system (and for the front, also the steering system). Furthermore, they must be internally sealed in such way so as to prevent any air flow from another
- Minor fixing details to permit the attachment of the Drum Deflectors described in Articles 3.13.5 and 13.6.
- An aperture contained within the periphery of the intersection between the Scoop defined in Article 3.13.3 and the
- Minor modifications to the front drum between ZW=155 and ZW=230, providing these are for the sole purpose of permitting the outboard suspension to connect to the upright and do not protrude from the original surface into the external air
3.13.3 Scoop
The Front and Rear Scoop must lie within RV-FWH-SCO and RV-RWH-SCO respectively.
Any part of the Scoop which is in contact with the external air stream must be tangent continuous and be fully visible when viewed parallel to the YW axis from inboard. These criteria will be assessed prior to the addition of apertures detailed in (c), (d) and (g).
Furthermore, with the exception of any Rear Scoop surfaces rearward of XW=0, the Scoop must satisfy the following criteria:
- For the parts of the Scoop’s surfaces that are visible when viewed parallel to the YW axis from inboard, the radius of curvature must be greater than
- Any intersection with a YW plane must produce only, a single closed section for the Front Scoop, and a single section for the Rear
Once the Front and Rear Scoop have been defined, they must be trimmed to RS-FWH-DRUM and RS-RWH-DRUM respectively, and a fillet radius no greater than 20mm may be applied at their boundaries.
Once the Front and Rear Scoops have been trimmed to their respective drums, the following apertures may be added:
- A single inlet aperture, with a periphery which:
- Must lie within RV-FWH-SCO and RV-RWH-SCO respectively and may not be more than 200mm when measured in ZW.
- Has no point more than 50mm from any other point on the periphery of the aperture when measured in XW and has no point rearward of XW= -100.
- A single outlet aperture, with a periphery which:
- Must lie within RV-FWH-SCO and RV-RWH-SCO respectively be fully visible from the rear and must lie above ZW= -50.
- For the Front Scoop, has no point more than 75mm from any other point on the periphery of the aperture when measured in XW and has no point forward of XW=100.
- For the Rear Scoop, has no point on the periphery of the aperture forward of XW=100
Once the Rear Scoop has been defined, trimmed to its drum, and the apertures permitted in
- and d. applied, the following geometry may be added:
- A single Rear Scoop Lip which must lie within RV-RWH-LIP. Furthermore:
- Its complete surface must be tangent continuous and contain no more than a single section in any XW
- For the parts of the Rear Scoop Lip surface that are visible when viewed parallel to the YW axis from inboard, the radius of curvature must be greater than 20mm. This is with the exception of regions of its surface that are within 5mm of the boundary of the Rear Scoop Lip when viewed parallel to the YW axis from inboard.
- A single Rear Scoop Lip which must lie within RV-RWH-LIP. Furthermore:
- Once the Rear Scoop Lip has been fully defined, it must be trimmed to the Rear Scoop and Rear Drum, such that no overlapping surfaces remain, and a fillet radius of no greater than 25mm may be applied at their boundaries. Once the fillet radius has been applied the external surfaces at the boundaries between adjacent sections of the Rear Scoop Lip and the Rear Scoop and Rear Drum must maintain tangent continuity in any XW, YW or ZW plane
- Once the requirements of paragraph e) above have been satisfied, additional geometry may be added to the combined rear drum and scoop surfaces, for the sole purpose of protecting the scoop inlet from debris ingestion, providing this geometry satisfies the following criteria:
- its entire surface sits within either RV-RWH-LIP or RV-RWH-SCP
- before the bodies are trimmed to the Rear Scoop, Rear Lip or Rear Drum, the additional geometry must not contain any open sections in any Xw, Yw and Zw planes
- on any Yw plane, any individual closed section must have a cross-sectional area less than 8mm2, with the exception of a fillet radius of no larger than 5mm at the boundaries.
Once the Front and Rear Scoop have been defined, trimmed to their respective Drums, had the apertures permitted in c. and d. applied, and in the case of the Rear Wheel Bodywork, the Rear Scoop Lip has been fully defined and trimmed to the Rear Scoop and Rear Drum, the following additional apertures may be added:
- Apertures for suspension members or suspension fairings. These apertures must be minimal in size in order to permit the full articulation of the suspension system (and for the front, also the steering system). Furthermore, they must be internally sealed in such way so as to prevent any air flow from another
With the exception of minimal incidental leakage, all and only air entering the inlet aperture described in point (c), must exit out of the outlet aperture described in point (d).
Furthermore, any flow line linking the inlet to the outlet must pass through a YW plane outboard of YW= -50, with the exception of ducts solely for cooling electrical components.
For clarity, apertures as referred to in this Article are considered to be mathematical surfaces that are coincident with the surfaces constructed in accordance with Article 3.13.3 and bound by their peripheries. Any criterion of visibility in this Article will consider these surfaces to be non-transparent.
3.13.4 Internal Cooling Ducts
Any bodywork which is situated within the volume defined by the drum and the scoop will be considered to be part of the internal Cooling Ducts and be classed as LTC.
3.13.5 Front Drum Deflector
The Front Drum Deflector must be made to the geometry defined by RS-FWH-DEFL.
In order to adapt the component of the Front Drum Deflector forward of XW= -30 to the local flow conditions, a +/-6° tolerance in its incidence will be accepted. Any such rotation must be made about a ZW-aligned axis through the point [XW= -260, YW= -10].
The parts of the permitted component above and below Zw= -110 may be adjusted as separate rigid bodies, by different amounts. To allow the parts of the resultant Front Drum Deflector to blend smoothly into one another, the angle of adjustment may vary within the regions between ZW= -110 and ZW= -70 and between ZW=110 and ZW=150. Within each of these two regions, the angle of adjustment must vary monotonically along ZW. The final surfaces must maintain both continuity and tangency across all boundaries of these regions. At ZW=150 continuity and tangency must be maintained to the Front Drum.
Bodywork may be added to further adapt the Front Drum Deflector components. Any such bodywork must:
- Lie within one of the following volumes. Each volume is defined by a four-sided simple polygon with vertices at the following points on YW=0, extruded along YW to the given value:
- [XW, ZW] = [-195, -130], [-195, -115], [-155, -115], [-155, -130], extruded to YW=50.
- [XW, ZW] = [-85, -182], [-85, -170], [-70, -170], [-70, -182], extruded to YW=100.
iii. [XW, ZW] = [27, -176], [41, -136], [81, -167], [77, -179], extruded to YW=56.
- [XW, ZW] = [79, -144], [88, -100], [135, -126], [132, -139], extruded to YW=60.
- [XW, ZW] = [28, -189], [32, -145], [92, -153], [88, -193] extruded to YW=106, with
regions outboard of YW=55 removed.
Existing regions of the Front Drum Deflector within the volumes defined in (iii), (iv) and
(v) may be trimmed away, provided that any new surfaces that result from the trim are not in contact with the external air stream once the added bodywork of this article is applied.
- Be solely for the purposes of adding flow aligned leading edges to the rearward component of the Front Drum Deflector, or adding flow aligned stays to the forward component.
- Not obscure any part of the Front Drum Deflector when viewed from the car centre plane. This applies only to bodywork within the volumes defined in (a.i) or (a.ii).
- In any YW plane:
- Maintain both continuity and tangency to the remaining Front Drum Deflector surfaces. This does not apply to bodywork within the volumes defined in (a.i) and (a.ii).
- Contain no more than one closed section in each volume defined in (a).
- Have no part of the section visible from above that is more than 15mm distant from the section visible from below. This does not apply to bodywork within the volume defined in (a.v).
- Have an XW-dimension of at least 30mm in each of the volumes defined in (a.iii), (a.iv) or (a.v), when combined with any remaining Front Deflector Surfaces within the same volume. This does not apply if the original geometry prior to the trimming permitted in (a) is below this minimum
- Have an XW-dimension no greater than 20mm. This applies only to bodywork within the volume defined in (a.i).
Once the added bodywork has been defined in accordance with this article, it is trimmed to RS-FWH-DRUM, the bodywork added in the volumes defined in (a.i) and (a.ii) is trimmed to Front Drum Deflector, and a fillet radius of no greater than 5mm may be added at the intersections between these surfaces. The resultant bodies are considered to be part of the Front Drum Deflector.
3.13.6 Rear Drum Deflector
The Rear Drum Deflector must be made to the geometry defined by RS-RWH-DEFL, with the exception of surfaces below the annotated curve “TRIM LINE” in RS-RWH-DEFL which may be trimmed. The part of the resulting trimmed Rear Drum Deflector below the annotated curve
“SINGLE SECTION LINE” in RS-RWH-DEFL must produce only a single section when intersected with any ZW or XW plane.
In order to adapt the Rear Drum Deflector to the local flow conditions, a +/-10mm tolerance in its ZW position and a +/-5° tolerance in its incidence about the annotated axis in
RS-RWH-DEFL will be accepted. Any translation in ZW includes the rotation axis and is applied before the rotation.
Once the Drum deflector has been positioned and adjusted in accordance with its specification, it must be trimmed to the Rear Drum and a maximum fillet radius, no greater than 5mm, may be applied along the intersections between these surfaces.
3.13.7 Wheel Cover
A single Wheel Cover per wheel, must be rigidly secured to the wheel rim such that it has the same rotational velocity as the wheel it is connected to and forms an aerodynamic seal to the wheel rim. The outboard surface of the Wheel Cover must be made to the geometry defined by RS-FWH-COV for the front wheels and by RS-RWH-COV for the rear wheels.
The Wheel Covers are classed as SSC.
3.14 Suspension Fairings
- Suspension Fairings must be fitted to all suspension members defined in Article 10.3.6, with the exception of those of circular cross
Each suspension fairing must:
- Fully cover the suspension member it corresponds to and any other components supported on it, such as hydraulic brake lines, electrical wiring and wheel tethers (all of which must be supported on a suspension member), over the span exposed to the external air
- Be rigid and rigidly secured to the suspension member (rigidly secured means not having any degree of freedom).
Minimal deformation will nonetheless be accepted for suspension conforming to Article
10.3.3. In such cases, any shared cover sections may deform or articulate a minimal amount to accommodate nominal misalignment of the relevant suspension members through the suspension travel range.
Furthermore, the surface bounded by the external cross-sections of each suspension fairing, when taken normal to the load line defined in Article 10.3.6 (a), must:
- Intersect the load line. With the exception of front suspension elements, locally, for the sole purpose of ensuring minimum clearance with the wheel rim at full steering
- Have at least one axis of symmetry, of which the larger one will be called the “major axis”.
- Have no dimension which exceeds 100mm, or 150mm only where a single fairing per side is used to shroud the driveshaft in addition to a suspension
- Up to two suspension fairings per side may be trimmed to allow the passage of the driveshaft. In such cases, compliance with the remainder of this Article must be demonstrated before the strictly necessary removal of any fairing material related to the passage of the
- Have an aspect ratio no greater than 3.5:1, that being defined as the ratio of the major axis to the maximum thickness, measured in the direction normal to the major axis. Furthermore, no dimension may be more than 5mm larger than the major
- Have an incidence (defined as the angle between the major axis and Z=0 with the car at its legality ride height, as defined in Article 10.1.4.) which lies within the following ranges:
- For the Front Suspension Fairings, between 10° (nose down) and 0°
- For the Rear Suspension Fairings, between 10° (nose down) and -10° (nose up)
- Fairings of suspension members which share an attachment point will be considered by a virtual dissection into discrete components. Such fairings will be allowed local minimal exceptions to Article 3.14.1 (d), (g) and (h) close to the junction of the suspension members, including minimal cut outs to allow the passage of a suspension member connected inboard to the rockers defined in Article 10.4.1. After application of any such cut out, the resultant fairings must still seal the internal volume of the fairings from the external
- The angle between the normal to any point of the surface of a suspension fairing and a plane normal to the corresponding suspension member’s load line must not exceed 15deg. Legitimate exceptions to this constraint will be accepted close to the inner and outer attachment points, or close to the junction between suspension members that share an attachment.
- In order to permit suspension travel while maintaining an aerodynamic seal, minimal flexible components may be fitted between the Suspension Fairings and the following components:
- The Front Bodywork defined in Article 6.
- The Tail Bodywork defined in Article 8.
- The Wheel Bodywork defined in Article 13.
- The gearbox case as defined in Article 1.7
- The suspension fairing covering the suspension member connected inboard to the rockers defined in Article 4.1.
With the car at its legality ride height, these flexible components must:
- Contain a fillet radius of up to 30mm between the components they are
- Other than the fillet radius described above, conform with the shape restrictions of either of the two components they are sealing to each other. For clarity, parts of these components may be replaced with the flexible
- Be designed in such way as to maintain their shape integrity with the car in motion, and as much as possible, with the suspension at another position than that of the Legality Ride
Minimal exceptions to (f) and (g) are permitted between the Suspension Fairings and the Front Wheel Bodywork and between the Fairing of the Front Trackrod and the Front Bodywork. These exceptions are for the sole purpose of introducing a pleat into the flexible component to allow steering articulation without compromising the structural integrity of the flexible component. With the suspension at the Legality Ride Height and wheels in the straight-ahead position, these pleats must be internal to the volume bound by the fillet radius referred to in (f) above.
3.15 Aerodynamic Component Flexibility
3.15.1 Introduction of load/deflection tests
In order to ensure that the requirements of Article 3.2.2 are respected, the FIA reserves the right to introduce further load/deflection tests on any part of the bodywork which appears to be (or is suspected of), moving whilst the car is in motion.
3.15.2 Load/deflection linearity
All load deflection tests must have a nominally linear elastic relationship unless otherwise stated.
3.15.3 Rear Wing Skins
The skins of the rear wing elements may deflect no more than 2mm when a 60N force is applied to the skin normal to and away from the element.
The force will be applied using a vacuum cup of 50mm diameter and the deflection will be measured at the outer diameter of the cup.
3.15.4 Front Wing Bodywork Flexibility
The flexibility of Front Wing Bodywork will be tested by applying a load of [0, 0, -1000]N at points [XF, Y, Z] = [-800, ±800, 250] or [-1000, ±800, 250].
The load will be applied in a downward direction using a 50mm diameter ram on a rectangular adaptor measuring 350mm in the X-direction and 150mm in the Y-direction. This adaptor must be supplied by the team and should:
- Have a flat top surface without
- Be fitted to the car so as to apply the full load to the bodywork at the test point and not to increase the rigidity of the parts being
- Be placed with the inner face 725mm from Y=0.
- Be placed with its forward face at XF=-1100mm.
- Be placed with its top face at Z=250
- Have a mass of no more than
The deflection will be measured relative to the survival cell and along the loading axis.
When the load is applied symmetrically to both sides of the car the vertical deflection must be no more than 15mm.
When the load is applied to only one side of the car the vertical deflection must be no more than 20mm.
3.15.5 Front Wing Flap Flexibility
Any part of the trailing edge of any front wing flap may deflect no more than 5mm, when measured along the loading axis, when a 60N point load is applied normal to the flap.
3.15.6 Front Floor Flexibility
Bodywork flexibility will be tested by applying a load vertically upwards using a 50mm diameter pad with a gimbled interface to the loadcell. The position of the centre of the pad will be given by the FIA and will be on the underside of the plank within a quadrilateral area, with vertices at points [XF=460, 50], [XF=610, 65], [XF=610, -65], [XF=460, -50]. The deflection will be measured along the loading axis.
At all times during the test, the load at a given deflection must exceed the load given by a straight-line graph defined by connecting the following coordinates in order: (0 mm, 0 N) (1 mm, 0 N) (5 mm, 4000N) (25mm, 6000N). This must be the case whether the deflection is increasing, decreasing, or held constant. The test will have no more than a maximum load of 8000N or a maximum deflection of 15mm (whichever is reached first) unless specifically requested by the FIA to investigate behaviour above these limits.
The load deflection relationship must be strictly monotonic with both increasing and decreasing deflection.
3.15.7 Outboard Floor Flexibility
- Bodywork may deflect no more than 5mm vertically when a [0, 0, -500]N load is applied to it at a position chosen by the Competitor, between XR=-450 and XR=-500, and Y=
±450. The load will be applied using a 50mm diameter ram and an adaptor of the same
size. Teams must supply the latter when such a test is deemed necessary.
- Bodywork may deflect no more than 20mm vertically when a [0, 0, 500]N load is applied to it at points [XR, Y] [-450, ±600] or [-1300, ±670]. The load will be applied using a 50mm diameter ram and an adaptor of the same size in an upwards or downwards direction. Teams must supply the latter when such a test is deemed
- The outboard edge of the Floor Bodywork Group may deflect no more than 8mm in Z at any point between XR = -1260 and XR = -350 when a distributed load of [0, 0, -600]N is applied to each side of the
The load will be applied simultaneously at 6 points on each side of the car, nominally at: [XR, Y] = [-480, 652.2], [-635, 686.3], [-790, 714.4], [-945, 736.7], [-1100, 753.3], and
[-1255, 764.2]. A 2mm tolerance on position will be permitted for manufacturing
reasons.
When viewed from above, and with the Floor Bodywork Group as fully defined in Article 3.5.6 in place, nothing other than the bodywork may be visible within 15mm of any load application point. A load application point that does not meet this requirement may be moved, in X and/or in Y, by the minimum amount necessary to comply. The FIA may require load points to be moved if, in their view, the load location or the floor shape has been specifically designed to permit greater levels of outboard floor flexibility in untested regions of the floor.
Once the load application positions are fully defined, Teams must provide a suitable means of applying the load to the upper surface of the bodywork. The load will be applied through a rod of diameter 2.3mm. Details of this arrangement are provided in the appendix to the Technical and Sporting Regulations. The contact of any load- spreader with the bodywork must lie within a cylinder of diameter 25mm, coaxial with the load application axis. If the Team’s preferred method requires through-holes, these holes must be sealed on either or both of the upper and lower surfaces at all times the car is on the circuit and during any assessment of any visibility from above around load application points.
Loads will be applied to these rods in two stages:
- [0, 0, -50]N to each load application point to give 300N per
- [0, 0, -100]N to each load application point to give 600N per
Deflection will be measured by laser scanning of the bodywork at each loading stage.
3.15.8 Central Floor Flexibility
- Bodywork within RV-PLANK may deflect no more than 2mm at the two holes in the plank at XF=1080 and no more than 2mm at the rearmost hole, when the car, without driver, is supported at these positions. The car will be supported on 70mm diameter pads, centred on the holes, and only in contact with the underside of the plank assembly. The displacement will be measured at the supports, relative to the reference plane at the centre of each
Furthermore, the stiffness for any deflection exceeding that defined in the previous paragraph must be no less than 15kN/mm.
Competitors will be required to demonstrate the local vertical stiffness and design installation of the skids and plank to the FIA for the regions around the periphery of each of these three holes. Compliance with Article 3.5.9.e. will only be assessed in the regions that are at least 90% as stiff as the stiffest part of the periphery. Any designs intended to protect these regions of the periphery from wear will not be accepted.
Competitors will be required to demonstrate compliance with these provisions by way of a detailed inspection of both the CAD and the physical installation, as well as Finite Element analysis.
- Bodywork on the reference plane may deflect no more than 0.2mm when the car, without driver, is supported at the two holes in the plank at XF=1080 and at the rearmost hole in the plank. The car will be supported on 40mm diameter pads, centred on the holes, and only contacting the bodywork on the reference plane. For the two holes at XF=1080 the displacement will be measured at the supports, relative to the survival cell datum points detailed in Article 3.2.6. For the rearmost hole the displacement will be measured at the support, relative to the power unit at the uppermost transmission mounting studs detailed in Article 4.8.
3.15.9 Rear Wing Mainplane Flexibility
- Bodywork may not deflect more than 6mm along the loading axis and 1.0° in a Y-plane, when two loads of [0, 0, -1000]N each, are applied simultaneously to the Rear Wing The loads will be applied at [XR=375, ±300, 910]
- Bodywork may not deflect more than 6mm along the loading axis and 1.0° in a Y-plane, when two loads of [324, 0, -940]N each, are applied simultaneously to the Rear Wing The loads will be applied at [XR=325, ±300, 900]
The loads in (a) and (b) will be applied through adaptors, supplied by the team, that lie between 250mm and 350mm from Y=0 and between XR=90 and at least XR=500. The upper surface each adaptor must lie at Z=910 and should have a counterbore of 52mm diameter for the application of the load in (b).
The angular deflection will be measured on the rear wing profiles, at [XR, Y] [350, ±150], and [350, ±450] and relative to the Rear Impact Structure. Teams must provide four pads to support tracking targets. Details of the targets is given in the Appendix to the Technical and Sporting Regulations.
The tests defined in this article may be performed with the RW Flap removed. In such cases the permitted deflections will be 25% higher than those defined in (a) and (b).
3.15.10 Rear Wing Flap Flexibility
The RW Flap may deflect no more than 7mm horizontally when a 500N load is applied horizontally. The load will be applied in the plane Z=875 at one of three separate points which lie within 50mm of the car centre plane and 270mm either side of it. The loads will be applied in a rearward direction using a suitable 25mm wide adaptor which must be supplied by the relevant team.
The deflection will be measured along the loading axis and relative to the forward part of the Rear Wing Mainplane at the same Y-station.
3.15.11 Rear Wing Mainplane Trailing Edge
The forward-most aerofoil element of Rear Wing Profiles may deflect no more than 3mm along the line of load application, when a 200N load is applied normal to the lower surface. The load will be applied in line with the trailing edge of the element at Y=0, Y=±125, or at Y=±375.
The deflection will be measured relative to the forward part of the Rear Wing Mainplane at the same Y-station.
The loads will be applied using a suitable adaptor, supplied by the relevant team, which:
- May be no more than 50mm
- Which extends no more than 10mm forward of the trailing
- Incorporates an 8mm female thread in the
3.15.12 Beam Wing Flexibility
No element within RV-RW-BEAM may deflect more than 3mm when a load of 150N is applied to its trailing edge, normal to the lower surface of the element. Two loads of 150N will be applied simultaneously at Y=270 and Y=-270 and 5mm forward (measured along the lower surface) of the local trailing edge.
The deflection will be measured along the line of load application, relative to the Rear Impact Structure.
The loads will be applied using adaptors, no more than 60mm wide, supplied by the relevant team. These adaptors must conform to the specification given in the Appendix to the Technical and Sporting Regulations.
3.15.13 Rear Wing Endplate Flexibility
The endplates described in article 3.10.4 may deflect no more than 10mm, when measured along the loading axis, when a 50N point load is applied in an inward direction normal to the
car centre plane using a spherical 15mm diameter tip at [XR, Z] = [635, 585]. For this measurement, the contribution of the rigid-body rotation of the whole wing assembly will be removed.
3.15.14 Front Drum Flexibility
Bodywork defined by RS-FWH-DRUM may deflect no more than 5mm, vertically, when a 60N load is applied vertically downwards at [XW=0, YW=-100, ZW=425]. The load will be applied using an adaptor provided by the FIA.
3.15.15 Rear Wing Slot Gap Deflection
With the hydraulic system active and the DRS deployed, a spherical gauge must not pass through the gap between the two elements within RV-RW-Profiles. The gauge will have a diameter of 85mm +0.00 / -0.05mm and a load of 10N will be applied during the test.
3.15.16 Additional Diagnostics
To allow the behaviour of the Rear Wing to be monitored using the onboard cameras, contrasting markers must be applied to bodywork within RV-RW-PROFILES and within RV- RW-BEAM. Details of these markers and their positions are given in the Appendix to the Technical and Sporting Regulations.
3.16 Aerodynamic Component construction
The components outlined below must be constructed to prescribed laminates. Details of these laminates can be found in Article 15.6.2.
3.16.1 Front Wing Endplate
The bodywork declared as Front Wing Endplate in Article 3.9.5 must be made to the laminate
PL-ANTI-SPLINTER.
Fasteners and related inserts, for the purpose of attaching the front wing endplate to the profiles must be positioned at least 30mm rearward of the leading edge of the endplate.
3.16.2 Suspension Fairings
Suspension Fairings as defined in Article 3.14 must be made to the laminate PL-SUS-FAIRING. Additional reinforcing plies may be added to this laminate where necessary.
- The secondary roll structure fairings, defined in Article 3.12.3, must be made to the laminate
PL-HALO